Aż 26802 odsłony sprawia, że wybór odpowiednich gazów ochronnych do spawania jest kluczową kwestią. W spawalnictwie gazy klasyfikowane są do dwóch grup – palnych i osłonowych. Właściwy dobór tych gazów ma ogromny wpływ na jakość i efektywność procesów spawalniczych, takich jak TIG, MIG oraz MAG.
Kluczowe wnioski:
- Gazy ochronne mają kluczowe znaczenie dla powodzenia procesu spawania
- Właściwy wybór gazu zależy od metody spawania i spawanego materiału
- Gazy palne i osłonowe różnią się zadaniami i właściwościami
- Parametry przepływu gazu osłonowego muszą być odpowiednio dobrane
- Czystość gazu ochronnego ma wpływ na jakość spoin
Wprowadzenie do gazów ochronnych
Gazy stosowane w procesie spawania można podzielić na dwie główne kategorie: gazy palne i gazy osłonowe. Gazy palne, takie jak propan (C3H8) i acetylen (C2H2), są wykorzystywane do podgrzewania lub prostowania elementów metalowych. Z kolei gazy osłonowe to grupa gazów technicznych, przemysłowych lub atmosferycznych, których zadaniem jest ochrona obszaru roboczego przed niekorzystnym działaniem pierwiastków i związków chemicznych podczas spawania.
Zadania gazów ochronnych w procesie spawania
Główne funkcje gazów ochronnych w spawaniu to:
- Ochrona jeziorka spawalniczego przed utlenianiem i zanieczyszczeniami
- Stabilizacja łuku elektrycznego
- Kontrola właściwości fizycznych i chemicznych spawu
- Poprawa jakości spoiny i wyglądu zewnętrznego
Rodzaje gazów ochronnych: palne i osłonowe
Gazy palne, takie jak propan i acetylen, mają zastosowanie w procesach spawania i lutowania gazowego. Z kolei gazy osłonowe, w skład których wchodzą m.in. tlen, dwutlenek węgla, azot i argon, są stosowane w metodach spawania łukowego MIG/MAG i TIG w celu ochrony jeziorka spawalniczego i obszaru roboczego.
Rodzaj gazu | Właściwości | Zastosowania |
---|---|---|
Propan (C3H8) | – Gaz palny – Bezbarwny i bezwonny | – Spawanie i lutowanie gazowe |
Acetylen (C2H2) | – Gaz palny – Bezbarwny i łatwopalny | – Spawanie i lutowanie gazowe |
Gazy osłonowe (tlen, CO2, N2, Ar) | – Zapewniają ochronę jeziorka spawalniczego – Stabilizują łuk elektryczny – Kontrolują właściwości fizyczne i chemiczne spawu | – Spawanie MIG/MAG i TIG |
Gazy palne i ich właściwości
W procesie spawania wykorzystywane są różnego rodzaju gazy palne, każdy z nich charakteryzuje się niepowtarzalnymi właściwościami i zastosowaniami. Dwa z nich, propan (C3H8) i acetylen (C2H2), odgrywają szczególną rolę w spawaniu i cięciu metali.
Propan (C3H8)
Propan to skroplony gaz węglowodorowy, który znajduje szerokie zastosowanie w spawaniu lutowanym, szczególnie przy łączeniu różnych materiałów. Dzięki wysokiej czystości spalania, propan jest idealnym wyborem do lutowania miękkiego, podgrzewania oraz formowania niewielkich elementów. Jego temperatura płomienia sięga nawet 1900°C, co czyni go wydajnym i efektywnym gazem dla tego typu zastosowań.
Acetylen (C2H2)
Acetylen to gaz palny, który jest często wykorzystywany w procesach cięcia dłuższych części, bez konieczności częstych przerw. W połączeniu z tlenem, acetylen zapewnia niezwykle wysoką temperaturę spalania, co pozwala na szybsze cięcie w porównaniu do propanu. Ponadto, acetylen jest cięższy od powietrza, co sprawia, że nadaje się również do spawania stali.
Zarówno propan, jak i acetylen, są jednymi z najważniejszych gazów palnych stosowanych w spawalnictwie. Każdy z nich ma swoje unikalne cechy i znajduje zastosowanie w różnych technikach łączenia metali.
Gazy osłonowe i ich zastosowanie
Gazy osłonowe odgrywają kluczową rolę w procesie spawania, zapewniając ochronę spawanego obszaru przed niekorzystnymi warunkami atmosferycznymi. Jednak ich rola nie ogranicza się tylko do tej funkcji – często mają one również istotny wpływ na przebieg procesu spawania oraz jakość uzyskanej spoiny.
Najczęściej stosowanymi gazami osłonowymi są: dwutlenek węgla (CO2), argon (Ar), hel (He), azot (N) oraz wodór (H). Każdy z nich lub ich mieszaniny posiada nieco inne właściwości, które determinują ich zastosowanie w różnych metodach spawania.
- Dwutlenek węgla znajduje zastosowanie m.in. przy spawaniu metodą MAG stali konstrukcyjnych niestopowych i niskostopowych.
- Argon jest używany w spawalnictwie metodami TIG i MIG oraz przy spawaniu metali o dużej aktywności chemicznej, takich jak tytan czy tantal.
- Hel najlepiej sprawdza się w spawaniu stopów aluminium ze względu na swoją wysoką przewodność cieplną.
- Azot stosowany jest głównie do spawania miedzi i stali austenitycznych.
- Wodór jest wykorzystywany w procesach spawania MIG i TIG, często mieszany z argonem w celu zwiększenia energii łuku i głębokości wtopienia.
Należy jednak pamiętać, że zastosowanie czystego dwutlenku węgla może generować odpryski i obniżać odporność spoin, dlatego często stosuje się mieszaniny gazów, dobrając ich proporcje do konkretnej metody spawania i materiału.
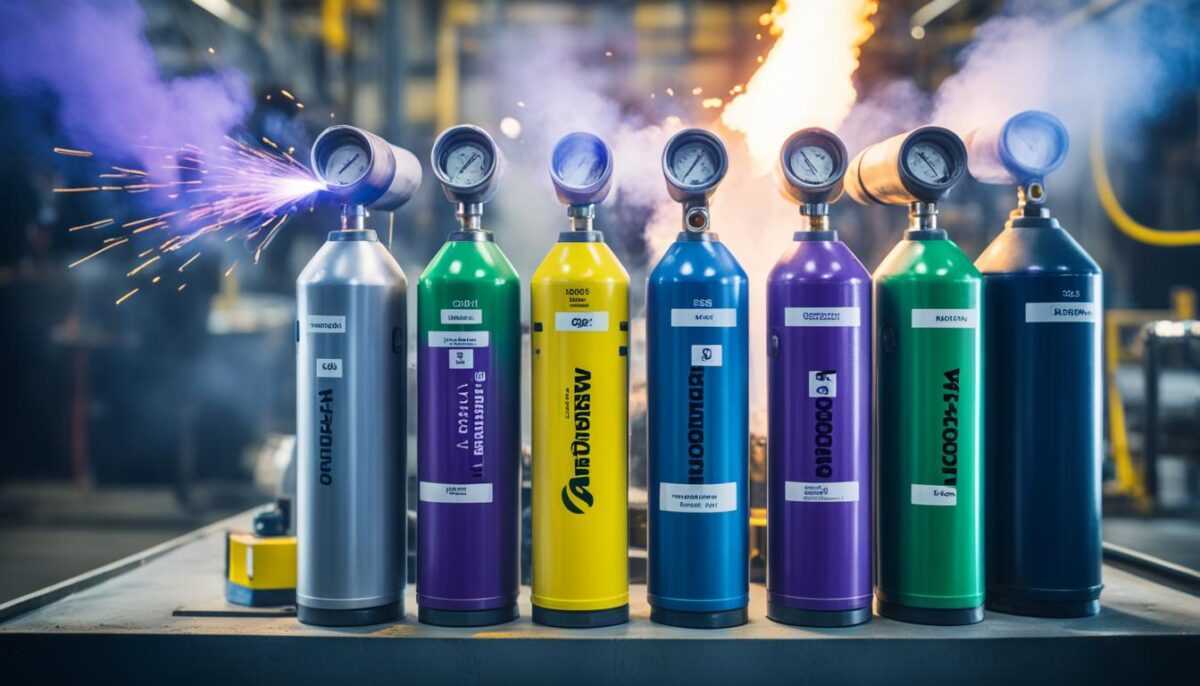
Wybór odpowiedniego gazu osłonowego ma kluczowe znaczenie dla wydajności procesu spawania oraz jakości uzyskanych połączeń. Dlatego też niezwykle istotne jest dopasowanie rodzaju i parametrów gazu do danej metody spawania oraz właściwości spawanego materiału.
Dobór gazu osłonowego do metody spawania
Wybór odpowiedniego gazu osłonowego ma kluczowe znaczenie dla przebiegu procesu spawania i jakości otrzymanej spoiny. Poszczególne metody spawania wymagają zastosowania właściwego rodzaju gazu.
Gazy do metody TIG
W spawaniu metodą TIG najczęściej wykorzystywany jest argon, który zapewnia stabilność łuku i dobrą ochronę spoiny. Innym popularnym gazem jest mieszanina argonu z helem, która pozwala uzyskać wyższą prędkość spawania i głębsze wtopianie.
Gazy do metody MIG
Podczas spawania metodą MIG również stosuje się gazy obojętne, takie jak argon, hel lub ich mieszanki. Gazy te chronią spieniającą się krawędź materiału podstawowego oraz stopioną elektrodę, zapewniając wysoką jakość spawania.
Gazy do metody MAG
Metoda MAG wymaga użycia gazów aktywnych, a więc dwutlenku węgla i mieszanin, w skład których wchodzą też inne gazy, np. argon i tlen. Tego typu mieszanki gazowe poprawiają stabilność łuku, ograniczają rozbryzgi i zapewniają estetyczny wygląd spoiny.
Właściwy dobór gazu osłonowego ma kluczowe znaczenie dla przebiegu procesu spawania i jakości otrzymanej spoiny. Wybór odpowiedniego gazu uzależniony jest od rodzaju spawanego materiału oraz metody spawania.
Spawanie gazowe i gazy do cięcia
Spawanie gazowe, zwane również autogenicznym, wykorzystuje płomień powstały na skutek spalania gazów palnych – głównie acetylenu (C2H2), a rzadziej propanu (C3H8) lub wodoru (H2) – oraz tlenu. Metoda ta znajduje zastosowanie w pracach remontowych i naprawczych, gdzie wymagana jest mobilność i prostota wykonania. W procesie cięcia plazmowego wykorzystuje się sprężone powietrze jako gaz roboczy, a czasami także azot. Z kolei cięcie gazowe polega na rozgrzewaniu stali do temperatury zapłonu i utlenieniu materiału pod wpływem tlenu pod wysokim ciśnieniem, przy użyciu acetylenu lub propanu do wstępnego nagrzewania.
Gazy do spawania gazowego
Acetylen (C2H2) jest głównym gazem stosowanym w procesie spawania gazowego. Jego wysoka energia cieplna pozwala na spawanie różnorodnych metali, takich jak niskostopowe stale, żeliwo czy brąz. W przypadku cięcia acetylenu używa się w połączeniu z tlenem, tworząc optymalny płomień o temperaturze do 3100°C.
Gazy do cięcia plazmowego i gazowego
W cięciu plazmowym wykorzystuje się sprężone powietrze lub azot jako gazy osłonowe. Powietrze jest tańsze, ale azot zapewnia lepszą jakość cięcia, zwłaszcza w przypadku metali reaktywnych, takich jak tytan czy nierdzewna stal. Z kolei w cięciu gazowym głównym gazem jest tlen, który w połączeniu z acetylenem lub propanem umożliwia nagrzewanie i utlenianie stali.
Właściwy dobór gazów ochronnych i cięcia jest kluczowy dla uzyskania wysokiej jakości połączeń spawalniczych oraz efektywnego cięcia. Znajomość właściwości i zastosowań poszczególnych gazów pozwala na optymalizację procesów i osiągnięcie zamierzonych efektów.
Czystość gazów osłonowych
Czystość gazów osłonowych, takich jak argon, ma kluczowe znaczenie w procesie spawania metodami TIG i MIG. Wyróżnia się trzy główne klasy czystości gazów osłonowych: 4.0, 4.5 oraz 5.0. Liczby te oznaczają odpowiednio 99,99%, 99,995% oraz 99,999% zawartości danego gazu w mieszaninie.
Wyższa czystość gazów spawalniczych jest często wymagana w specjalistycznych zastosowaniach, jednak wiąże się również z wyższymi kosztami. Dlatego ważne jest zrównoważenie wymagań jakościowych z możliwościami budżetowymi podczas wyboru odpowiedniego gazu osłonowego.
Klasy czystości gazów
- Klasa 4.0: 99,99% czystości gazu
- Klasa 4.5: 99,995% czystości gazu
- Klasa 5.0: 99,999% czystości gazu
Wyższa klasa czystości gazów osłonowych zapewnia wyższą jakość spawania, ale generuje również wyższe koszty. Decyzja o wyborze właściwej klasy zależy od konkretnych wymagań technologicznych i budżetowych projektu.
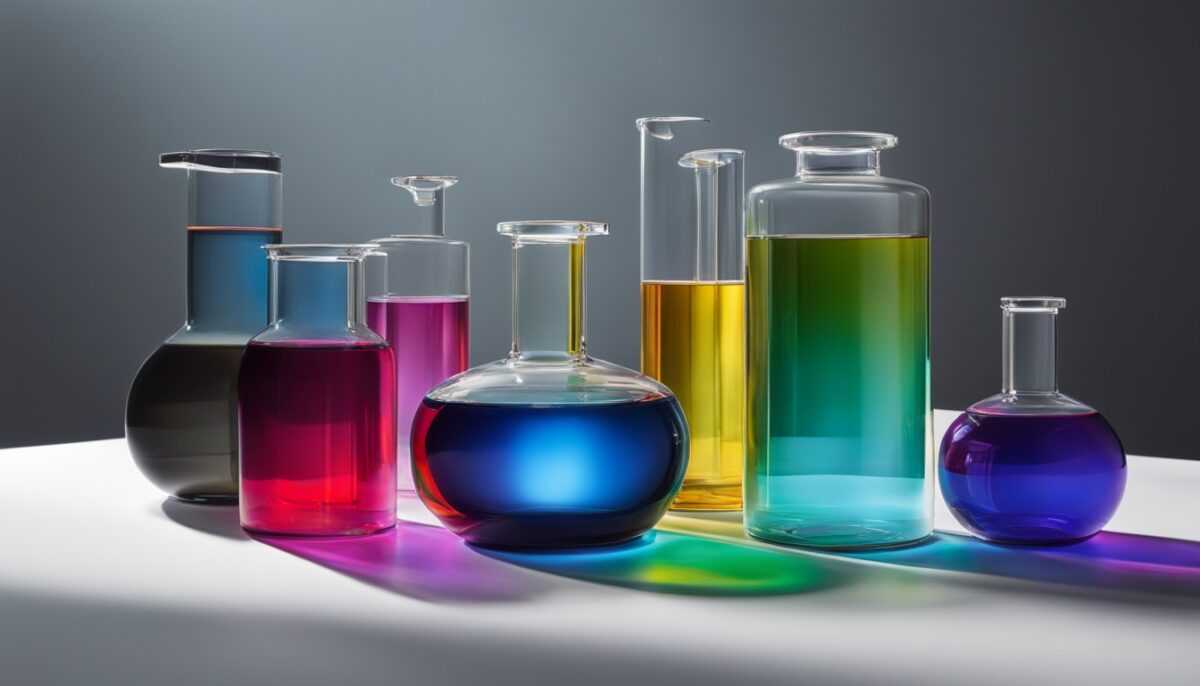
„Czystość gazów osłonowych jest kluczowa dla uzyskania wysokiej jakości spoin, szczególnie w spawaniu metodami TIG i MIG.”
Dobór przepływu gazu osłonowego
Odpowiedni przepływ gazu osłonowego ma kluczowe znaczenie dla przebiegu procesu spawania. W metodzie MIG/MAG przepływ gazu zwykle wynosi od 15 do 25 l/min, natomiast w spawaniu TIG jest on nieco mniejszy, od 5 do 15 l/min. Ogólna zasada mówi, że na każdy milimetr średnicy dyszy przypada 1 l/min przepływu gazu.
Jednak faktyczny optymalny przepływ zależy od wielu czynników, takich jak rodzaj gazu, materiał, technika spawania i warunki środowiskowe, dlatego warto konsultować się z instrukcjami producenta lub doświadczonym spawaczem. Na przykład, dla drutu o średnicy 1,6 mm przepływ gazu osłonowego powinien wynosić 16 l/min.
- Dla drutu o średnicy 0,6-0,8 mm minimalny przepływ gazu to 6-7 l/min, typowy to 8,5-10 l/min, a maksymalny to 14 l/min.
- Wartość napięcia łuku spawalniczego oraz prędkość podawania drutu mają istotny wpływ na jakość spoiny.
- Podczas spawania MIG/MAG wykorzystuje się prąd stały o biegunowości dodatniej.
Odpowiedni dobór gazu osłonowego ma zasadnicze znaczenie dla ochrony obszaru spawania oraz ostatecznych efektów spawania.
Warto pamiętać, że prawidłowe wdmuchnięcie gazu osłonowego może skutecznie zminimalizować rozpryski powstające podczas procesu spawania, a prawidłowe przedmuchanie gazu osłonowego może zmniejszyć porowatość spoiny. Natomiast dobór niewłaściwego rodzaju gazu może doprowadzić do pęknięć w spoinie oraz do pogorszenia właściwości mechanicznych.
Wybór odpowiednich gazów ochronnych
Wybór właściwego gazu ochronnego do procesu spawania jest kluczowym elementem, który ma znaczący wpływ na jakość i przebieg spawania. Gazy osłonowe odgrywają istotną rolę w ochronie spawanego materiału, kształtowaniu jeziorka spawalniczego oraz uzyskaniu pożądanych właściwości spoiny. Dlatego wybór gazów ochronnych powinien być dokonywany z należytą uwagą, biorąc pod uwagę różne czynniki, takie jak rodzaj spawanego materiału, metodę spawania oraz wymagania dotyczące jakości złącza.
Metody spawania w osłonach gazowych, takie jak MAG (Metal Active Gas), MIG (Metal Inert Gas) oraz TIG (Tungsten Inert Gas), wykorzystują gazy aktywne lub obojętne w celu ochrony jeziorka spawalniczego. Wybór odpowiedniego dobór gazów spawalniczych do każdej z tych metod jest kluczowy, aby uzyskać wysokiej jakości spoinę.
- Metoda MAG wykorzystuje dwutlenek węgla lub mieszanki argonu, tlenu i dwutlenku węgla do spawania stali niestopowych, niskostopowych i wysokostopowych.
- Metoda MIG używa gazów obojętnych, takich jak argon i hel, i stosowana jest do metali nieżelaznych.
- Metoda TIG, również z gazami obojętnymi, przeznaczona jest dla metali nieżelaznych oraz stali niskostopowej i wysokostopowej.
Argon jest najpopularniejszym i najbardziej powszechnym gazem spawalniczym, stosowanym w różnych metodach spawania. Hel natomiast znajduje zastosowanie szczególnie do spawania metali o dużych grubościach, takich jak aluminium czy stopy miedzi. Wybór odpowiednich gazów ochronnych ma kluczowe znaczenie dla uzyskania wysokiej jakości spoin i skuteczności całego procesu spawania.
Wniosek
Odpowiedni dobór gazów ochronnych do procesu spawania ma kluczowe znaczenie dla zapewnienia wysokiej jakości połączeń. Poznanie specyfiki i zastosowań różnych gazów spawalniczych, zarówno palnych, jak i osłonowych, pozwala na optymalizację tego procesu. Ważne jest również zwrócenie uwagi na czystość stosowanych gazów oraz właściwy dobór przepływu, aby zapewnić optymalną ochronę strefy spawania.
Podsumowując, podsumowanie wyboru gazów ochronnych jest niezbędne do uzyskania wysokiej jakości spoiny. Właściwe wykorzystanie gazów palnych i osłonowych, przy zachowaniu odpowiednich parametrów, takich jak czystość i przepływ, gwarantuje stabilność łuku elektrycznego oraz zapewnia ochronę materiału spawanego.
Niezwykle istotne jest również sporządzenie kompletnego wniosku o wydanie pozwolenia na wprowadzanie gazów lub pyłów do powietrza, zawierającego wszystkie niezbędne informacje dotyczące instalacji, emisji, monitorowania oraz działań na rzecz ochrony środowiska. Tylko w ten sposób można uzyskać niezbędne zezwolenia i legalnie prowadzić działalność produkcyjną.
FAQ
Jakie są zadania gazów ochronnych w procesie spawania?
Gazy ochronne zapewniają ochronę stopionego i rozgrzanego materiału przed wpływem powietrza atmosferycznego, a także tworzą korzystne środowisko dla powstawania i utrzymania łuku elektrycznego, który jest nieodzownym elementem procesu spawania.
Jakie rodzaje gazów ochronnych występują?
Gazy ochronne klasyfikowane są do dwóch grup – palnych i osłonowych. Gazy palne, takie jak propan i acetylen, są stosowane do podgrzewania lub prostowania elementów metalowych. Gazy osłonowe, takie jak argon, dwutlenek węgla czy azot, mają za zadanie ochronę obszaru roboczego podczas spawania.
Jakie są właściwości propanu i acetylenu?
Propan (C3H8) charakteryzuje się wysoką czystością spalania i znajduje zastosowanie przy lutowaniu twardym, miękkim, podgrzewaniu i formowaniu elementów. Acetylen (C2H2) zapewnia wysoką temperaturę spalania, co umożliwia szybsze cięcie niż przy użyciu propanu. Acetylen jest cięższy od powietrza atmosferycznego i nadaje się do spawania stali.
Jakie gazy osłonowe są najczęściej stosowane w różnych metodach spawania?
W spawaniu metodą TIG najczęściej używany jest argon lub mieszanina argonu z helem. Podczas spawania MIG stosuje się gazy obojętne, takie jak argon, hel lub ich mieszanki. Metoda MAG wymaga użycia gazów aktywnych, takich jak dwutlenek węgla i mieszaniny, w skład których wchodzą także inne gazy, np. argon i tlen.
Jakie gazy są stosowane w spawaniu gazowym i cięciu?
W spawaniu gazowym, zwanym autogenicznym, wykorzystuje się głównie acetylen, a rzadziej propan lub wodór. Cięcie plazmowe wykorzystuje sprężone powietrze jako gaz roboczy, czasami stosuje się także azot. Cięcie gazowe polega na rozgrzewaniu stali do temperatury zapłonu i utlenieniu materiału pod wpływem tlenu pod wysokim ciśnieniem, przy użyciu acetylenu lub propanu do rozgrzewania.
Jaka jest rola czystości gazów osłonowych w spawaniu?
Czystość gazów osłonowych, takich jak argon, ma duże znaczenie w spawaniu metodami TIG i MIG. Wyróżnia się klasy czystości 4.0, 4.5 oraz 5.0, które oznaczają odpowiednio 99,99%, 99,995% oraz 99,999% zawartości danego gazu w mieszaninie. Wyższa czystość jest często wymagana w specjalistycznych zastosowaniach.
Jak dobrać właściwy przepływ gazu osłonowego?
Ogólna zasada mówi, że na każdy milimetr średnicy dyszy przypada 1 l/min przepływu gazu. W metodzie MIG/MAG przepływ gazu zwykle wynosi od 15 do 25 l/min, natomiast w spawaniu TIG jest on nieco mniejszy, od 5 do 15 l/min. Jednak faktyczny optymalny przepływ zależy od wielu czynników, takich jak rodzaj gazu, materiał, technika spawania i warunki środowiskowe.
Jakie czynniki należy uwzględnić przy wyborze odpowiedniego gazu ochronnego?
Wybór odpowiedniego gazu ochronnego do procesu spawania zależy od rodzaju spawanego materiału, metody spawania oraz wymagań dotyczących jakości spoiny. Gazy osłonowe mają istotny wpływ na przebieg procesu spawania i właściwości uzyskanej złącza, dlatego kluczowe jest poznanie specyfiki poszczególnych gazów i dobranie ich do konkretnego zastosowania.