Według najnowszych statystyk, nowoczesne centra obróbcze wyposażone są w zaawansowane systemy sterowania, umożliwiając realizację skomplikowanych operacji z niespotykaną dotąd dokładnością i powtarzalnością. Ten imponujący rozwój technologii cyfrowych, takich jak Internet Rzeczy (IoT), sztuczna inteligencja (AI) czy uczenie maszynowe (ML), znajduje swoje odzwierciedlenie w sektorze maszyn CNC, znacząco transformując cały przemysł wytwórczy.
W niniejszym artykule przyjrzymy się najnowszym trendom i innowacjom w dziedzinie nowoczesnych maszyn CNC, które definiują kierunki rozwoju branży obróbki skrawaniem. Odkryjemy, w jaki sposób najnowsze narzędzia CNC wpływają na zwiększenie precyzji, efektywności oraz możliwości produkcyjnych w centrach obróbczych CNC.
Kluczowe wnioski:
- Rozwój technologii cyfrowych, takich jak IoT, AI i ML, napędza innowacje w sektorze maszyn CNC.
- Nowoczesne centra obróbcze oferują zaawansowane systemy sterowania umożliwiające precyzyjną i powtarzalną obróbkę.
- Integracja systemów CNC z IoT wspiera zdalny monitoring i kontrolę procesów produkcyjnych.
- Zastosowanie nowych materiałów i powłok narzędzi skrawających zwiększa ich wydajność i trwałość.
- Algorytmy AI i uczenia maszynowego optymalizują procesy obróbcze, przewidują błędy i dostosowują parametry cięcia.
Wprowadzenie do obróbki skrawaniem i roli maszyn CNC
Technologie cyfrowe odgrywają kluczową rolę w rozwoju obróbki skrawaniem w przemyśle. Nowoczesne maszyny CNC wyposażone są w zaawansowane systemy sterowania, które znacząco zwiększają precyzję, wydajność i elastyczność procesów produkcyjnych. Rozwój obróbki skrawaniem oraz innowacje w maszynach CNC umożliwiają produkcję coraz bardziej złożonych elementów, skracając jednocześnie czas i obniżając koszty wytwarzania.
Innowacje w obróbce skrawaniem i ich wpływ na rozwój przemysłu
Technologia 5-osiowa w obrabiarkach CNC umożliwia obróbkę skomplikowanych geometrii, redukując liczbę potrzebnych ustawień i zwiększając precyzję wytwarzanych części. Automatyzacja i integracja rozwiązań opartych na sztucznej inteligencji pozwalają na optymalizację parametrów obróbki w czasie rzeczywistym, minimalizując błędy i zwiększając efektywność produkcji.
Ponadto, nowe technologie chłodzenia i smarowania narzędzi skrawających poprawiają ich wydajność i trwałość, ograniczając tarcie i zużycie. Integracja systemów CAD/CAM z maszynami CNC skraca czas programowania i ustawiania, umożliwiając jednocześnie tworzenie bardziej zaawansowanych geometrycznie projektów.
Transformacja rynku maszyn CNC dzięki nowym technologiom
Rozwój technologii cyfrowych w przemyśle, takich jak Internet Rzeczy (IoT) i uczenie maszynowe (ML), wpływa na transformację rynku maszyn CNC. Nowoczesne systemy sterowania pozwalają na dokładne monitorowanie pracy maszyn, optymalizację procesów produkcyjnych i minimalizację zużycia narzędzi. Dodatkowo, integracja różnych technologii, takich jak druk 3D czy obróbka hybrydowa, zwiększa elastyczność i personalizację produkcji.
Efektem tych innowacji jest zwiększenie produktywności, redukcja błędów, a także oszczędności materiałowe i energetyczne w sektorach, takich jak lotnictwo, motoryzacja czy produkcja sprzętu medycznego, gdzie maszyny CNC odgrywają kluczową rolę.
Przełomowe technologie w nowoczesnych maszynach CNC
Współczesne nowoczesne maszyny CNC cechują się szeregiem innowacyjnych funkcji, które wpływają na wydajność, precyzję i niezawodność obróbki skrawaniem. Jednym z kluczowych osiągnięć jest integracja zaawansowanych systemów sterowania, które umożliwiają precyzyjne i szybkie przetwarzanie danych wejściowych na ruchy narzędzi maszyn. Dzięki temu możliwe jest wykonanie bardzo skomplikowanych części z zachowaniem wysokiej precyzji obróbki skrawaniem.
Zaawansowane systemy sterowania i precyzyjne przetwarzanie danych
Nowoczesne systemy sterowania CNC zapewniają szereg kluczowych funkcji, takich jak:
- Szybkie przetwarzanie sygnałów sprzętowych i optymalizacja trajektorii narzędzi
- Precyzyjna regulacja prędkości, przyspieszenia i położenia elementów ruchomych
- Wydajne algorytmy interpolacji liniowej, kołowej i przestrzennej
- Możliwość adaptacji do zmieniających się warunków obróbki w czasie rzeczywistym
Sztuczna inteligencja i uczenie maszynowe w optymalizacji procesów skrawania
Kolejnym przełomem w dziedzinie nowoczesnych maszyn CNC jest zastosowanie AI i ML. Zaawansowane algorytmy uczenia maszynowego pozwalają na optymalizację procesów skrawania, automatyczne dostosowywanie parametrów cięcia do zmieniających się warunków pracy oraz przewidywanie potencjalnych błędów przed ich wystąpieniem. Dzięki temu możliwe jest uzyskanie jeszcze wyższej precyzji obróbki skrawaniem przy jednoczesnej poprawie wydajności i niezawodności produkcji.
„Zastosowanie technologii CNC w kamieniarstwie przyczynia się do zwiększonej precyzji i dokładności wykonania, zapewniając doskonałą jakość wyrobów.”
Nowoczesne maszyny CNC, wyposażone w zaawansowane systemy sterowania oraz rozwiązania AI i ML, pozwalają na realizację coraz bardziej skomplikowanych i wymagających zadań obróbki skrawaniem. Branża przemysłowa znacznie zyskuje na wdrażaniu tych przełomowych technologii.
Integracja technologii bezprzewodowej i Internetu Rzeczy (IoT)
Rewolucja w świecie maszyn CNC napędzana jest przez technologie bezprzewodowe i Internet Rzeczy (IoT). Wprowadzenie tych innowacji umożliwiło zdalny monitoring i kontrolę procesów produkcyjnych, otwierając nowe możliwości dla operatorów maszyn. Dzięki temu mogą oni śledzić stan maszyny w czasie rzeczywistym i szybko reagować na wszelkie nieprawidłowości.
Technologie bezprzewodowe maszyny CNC i IoT w maszynach CNC znacząco ułatwiają również zdalne diagnostykę i serwisowanie obrabiarek. Przestoje w produkcji zostają zminimalizowane, a operatorzy uzyskują pełną kontrolę nad procesem obróbki, nawet z dala od samej maszyny.
Zastosowanie zdalnego monitoringu i kontroli procesów przynosi wiele korzyści, takich jak:
- Zwiększenie wydajności i efektywności produkcji
- Szybsza reakcja na problemy i usterki
- Lepsze wykorzystanie zasobów i obniżenie kosztów operacyjnych
- Zwiększenie bezpieczeństwa personelu poprzez ograniczenie bezpośredniego kontaktu z maszynami
Innowacje w dziedzinie bezprzewodowych maszyn CNC i IoT kształtują nową erę w przemyśle obróbki skrawaniem, otwierając drogę do wydajniejszej, zdalnie kontrolowanej produkcji.
Systemy chłodzenia i nowe materiały narzędzi skrawających
Nowoczesne maszyny CNC są wyposażone w zaawansowane systemy chłodzenia oraz smarowania narzędzi skrawających. Te rozwiązania mają istotny wpływ na jakość obróbki i trwałość maszyny. Zastosowanie innowacyjnych materiałów i powłok dla narzędzi skrawających pozwala na pracę przy wyższych prędkościach cięcia, a także znacznie zwiększa ich odporność na zużycie.
Wpływ zaawansowanych systemów chłodzenia na jakość obróbki
Wydajne systemy chłodzenia umożliwiają utrzymanie optymalnej temperatury narzędzi skrawających podczas obróbki, co przekłada się na:
- Zwiększenie trwałości i żywotności narzędzi
- Poprawę jakości powierzchni obrabianego elementu
- Zwiększenie prędkości skrawania i wydajności procesu
- Redukcję naprężeń cieplnych w obrabianym materiale
Innowacyjne powłoki i materiały dla narzędzi skrawających
Stale rozwija się rynek nowoczesnych materiałów i powłok dla narzędzi skrawających. Ich zastosowanie ma kluczowy wpływ na:
- Zwiększenie odporności na zużycie i wysoka trwałość
- Możliwość pracy z wyższymi prędkościami skrawania
- Poprawę jakości obrabianej powierzchni
- Wzrost wydajności procesów obróbki skrawaniem
Materiał narzędzia | Typowe zastosowania | Zalety |
---|---|---|
Węglik spiekany | Toczenie, frezowanie, wiercenie | Wytrzymałość, trwałość, odporność na ścieranie |
Ceramika | Toczenie, frezowanie, szlifowanie | Wysoka twardość, odporność na wysokie temperatury |
CBN (Cubic Boron Nitride) | Toczenie, frezowanie elementów hartowanych | Doskonała odporność na ścieranie, wysoka trwałość |
Diament | Toczenie, frezowanie, szlifowanie plastików i kompozytów | Najwyższa twardość, idealna dla materiałów ścieralnych |
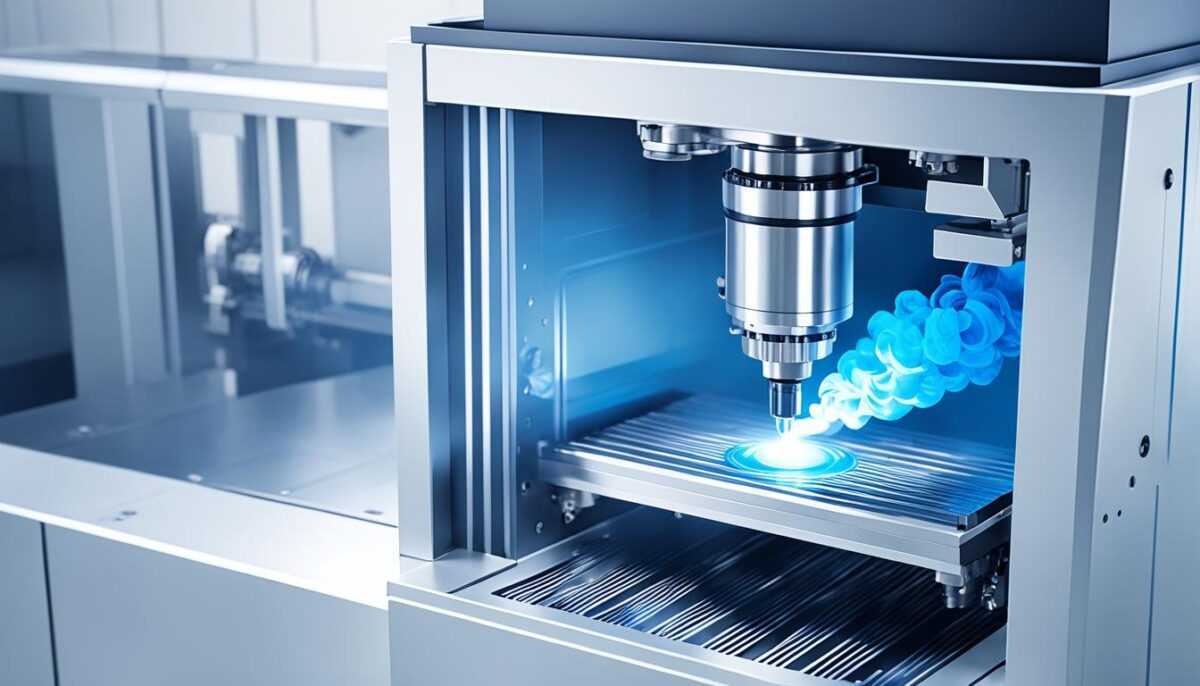
„Zastosowanie nowych materiałów i powłok dla narzędzi skrawających pozwala na pracę przy wyższych prędkościach cięcia oraz zwiększa odporność na zużycie.”
Inteligentne systemy sterowania w obrabiarkach CNC
Jedną z najważniejszych innowacji w dziedzinie sterowania obrabiarek CNC jest wykorzystanie algorytmów uczenia maszynowego. Technologie te pozwalają na optymalizację procesów skrawania poprzez ciągłą analizę danych zbieranych w czasie rzeczywistym. Dzięki temu systemy sterowania mogą samodzielnie dostosowywać parametry cięcia, takie jak prędkość posuwu, głębokość skrawania czy prędkość obrotową wrzeciona. Przekłada się to na wydłużenie żywotności narzędzi, poprawę jakości wykonywanych detali oraz zwiększenie ogólnej efektywności produkcji.
Algorytmy uczenia maszynowego w optymalizacji procesów skrawania
Zaawansowane systemy sterowania opartego na uczeniu maszynowym analizują dane z czujników zainstalowanych na obrabiarce, takie jak siła skrawania, drgania wrzeciona czy temperatura. Na podstawie zebranych informacji algorytmy adaptują i optymalizują parametry obróbki, nieustannie dążąc do uzyskania najwyższej wydajności i jakości procesu. Dzięki temu inteligentne systemy CNC stają się coraz bardziej autonomiczne i samodzielne w podejmowaniu optymalnych decyzji.
Korzyści z zastosowania uczenia maszynowego w obrabiarkach CNC | Przykłady praktycznego zastosowania |
---|---|
|
|
Zastosowanie inteligentnych systemów sterowania opartych na uczeniu maszynowym otwiera nowe możliwości w zakresie optymalizacji procesów skrawania w obrabiarkach CNC. Dzięki ciągłemu monitorowaniu i adaptacji parametrów obróbki, producenci mogą osiągnąć znaczne oszczędności, zwiększyć wydajność i poprawić jakość wytwarzanych detali.
Integracja systemów sterowania CNC z Internetem Rzeczy (IoT)
Dynamiczny rozwój technologii cyfrowych, takich jak Internet Rzeczy (IoT) i sztuczna inteligencja (AI), otwiera nowe możliwości w dziedzinie obróbki skrawaniem. Integracja systemów sterowania CNC z siecią IoT umożliwia zdalny monitoring i kontrolę pracy obrabiarek, a także automatyczną wymianę danych między różnymi urządzeniami w ramach inteligentnych fabryk. Ta synergia sprzętu i oprogramowania stanowi klucz do pełnej automatyzacji produkcji oraz efektywniejszego zarządzania zasobami.
Adaptacyjne systemy CNC wykorzystujące algorytmy AI i uczenia maszynowego pozwalają na automatyczną optymalizację procesów produkcyjnych. Inteligentne systemy CNC zwiększają wydajność, pracując z większą prędkością i precyzją, a jednocześnie redukując zużycie narzędzi i materiałów. Dzięki integracji IoT z obrabiarkami CNC można zbierać kompleksowe dane o pracy maszyn, co przekłada się na poprawę efektywności oraz minimalizację przestojów, obniżając koszty operacyjne.
- Rozwój technologii IoT i AI otwiera nowe perspektywy dla programowania maszyn CNC
- Integracja CNC z IoT oraz AI przyczynia się do przedłużenia żywotności narzędzi i maszyn
- Adaptacyjne systemy CNC wykorzystują algorytmy sztucznej inteligencji i uczenia maszynowego
- Inteligentne systemy CNC zwiększają efektywność, precyzję i redukują zużycie
- Integracja IoT z maszynami CNC umożliwia zbieranie danych i poprawę efektywności
Konwergencja Internetu Rzeczy (IoT) z technologią CNC otwiera drogę do monitorowania i optymalizacji procesów produkcyjnych w czasie rzeczywistym, zwiększając efektywność całej linii produkcyjnej. Firmy coraz chętniej inwestują w automatyzację procesów frezarskich, co przyczynia się do wzrostu wydajności i precyzji obróbki.
„Zastosowanie IoT w systemach CNC sprzyja rozwojowi usług opartych na modelu predykcyjnym, pomagając w przewidywaniu awarii i zwiększając niezawodność procesu produkcyjnego.”
Zaawansowane interfejsy użytkownika i symulacje cyfrowe
Współczesne maszyny CNC są wyposażone w niezwykle zaawansowane interfejsy graficzne użytkownika (GUI), które znacznie ułatwiają ich obsługę. Intuicyjność tych systemów pozwala na szybsze przyswojenie umiejętności przez mniej doświadczonych operatorów, skracając czas potrzebny na szkolenie personelu.
Dodatkowo, symulacje cyfrowe procesów produkcyjnych umożliwiają przetestowanie nowych programów obróbczych przed ich rzeczywistym wdrożeniem. Dzięki temu możliwe jest szybsze uruchamianie maszyn i zwiększenie wydajności całego procesu.
Nowoczesne systemy sterowania maszynami CNC oferują także zaawansowane funkcje wspomagania decyzji, które optymalizują ergonomię stanowisk pracy i znacznie podnoszą komfort obsługi. Przekłada się to na wyższą jakość i efektywność produkcji.
Funkcja | Korzyści |
---|---|
Intuicyjne interfejsy graficzne (GUI) | Łatwiejsza obsługa dla mniej doświadczonych operatorów, skrócenie czasu szkolenia |
Symulacje cyfrowe procesów produkcyjnych | Szybsze uruchomienie nowych programów obróbczych, zwiększenie wydajności |
Wspomaganie decyzji przez system | Optymalizacja ergonomii stanowisk pracy, poprawa komfortu obsługi |
Zaawansowane interfejsy użytkownika i symulacje cyfrowe to kluczowe elementy nowoczesnych maszyn CNC, które wspierają obsługę, skracają czas uruchomienia nowych programów i podnoszą jakość produkcji.
Technologie adaptacyjnego sterowania procesami skrawania
Wraz z rozwojem nowoczesnych maszyn CNC, wprowadzane są coraz bardziej zaawansowane technologie adaptacyjnego sterowania procesami skrawania. Te innowacyjne systemy reagują w czasie rzeczywistym na zmieniające się warunki obróbki, kompensując wpływ czynników takich jak zużycie narzędzia czy wahania temperatury materiału obrabianego.
Dzięki temu technologie te zapewniają stałą, wysoką jakość produktu końcowego, bez konieczności ciągłej ingerencji operatora. Kluczowe funkcje tych systemów to adaptacyjne sterowanie posuwem, kompensacja zużycia narzędzi oraz optymalizacja parametrów skrawania.
- Adaptacyjne sterowanie posuwem umożliwia dynamiczne dostosowanie prędkości posuwu do aktualnego obciążenia narzędzia, co zwiększa wydajność i przedłuża żywotność narzędzi.
- Kompensacja zużycia narzędzi koryguje parametry obróbki w celu utrzymania stałej jakości powierzchni, nawet przy postępującym zużyciu narzędzia.
- Optymalizacja parametrów skrawania, oparta na systemach predykcyjnych, pozwala uzyskać optymalny balans między wydajnością a trwałością narzędzia.
Zastosowanie tych technologii adaptacyjnych w obróbce skrawaniem przynosi wymierne korzyści, takie jak zwiększenie produktywności, poprawa jakości wyrobów oraz redukcja kosztów produkcji. Są to kluczowe czynniki wpływające na konkurencyjność nowoczesnych przedsiębiorstw przemysłowych.
„Technologie adaptacyjnego sterowania procesami skrawania umożliwiają produkcję wyrobów o stałej wysokiej jakości, bez konieczności ciągłej kontroli przez operatora.”
Wdrożenie tych zaawansowanych systemów jest istotnym krokiem w kierunku inteligentnej i elastycznej produkcji, opartej na adaptacyjnym sterowaniu procesami skrawania, kompensacji zużycia narzędzi oraz optymalizacji jakości produktu końcowego.
Ekologiczne i energooszczędne rozwiązania w maszynach CNC
Współczesne maszyny CNC odgrywają kluczową rolę w rozwoju zrównoważonej produkcji dzięki innowacjom w zakresie ekologicznych i energooszczędnych rozwiązań. Jednym z ważnych obszarów jest optymalizacja procesów cięcia i redukcja odpadów.
Optymalizacja procesów cięcia i redukcja odpadów
Zaawansowane systemy sterowania w maszynach CNC pozwalają na precyzyjne planowanie trajektorii narzędzia, minimalizując ilość odpadów i zużycie materiału. Nowoczesne oprogramowanie umożliwia dokładną symulację i optymalizację procesów skrawania, co przekłada się na znaczne oszczędności surowców.
Napędy elektryczne o wysokiej sprawności energetycznej
Kolejnym istotnym trendem jest zastępowanie tradycyjnych hydraulicznych systemów napędowych napędami elektrycznymi o wysokiej sprawności energetycznej. Rozwiązania te charakteryzują się znacznie niższymi stratami energii, przyczyniając się do zwiększenia efektywności energetycznej obrabiarek CNC.
Parametr | Maszyna CNC z hydrauliką | Maszyna CNC z napędem elektrycznym |
---|---|---|
Zużycie energii | Wyższe | Niższe |
Hałas | Wyższy | Niższy |
Konserwacja | Wyższa | Niższa |
Sprawność energetyczna | Niższa | Wyższa |
Podsumowując, ekologiczne i energooszczędne rozwiązania w maszynach CNC, takie jak optymalizacja procesów cięcia i wykorzystanie napędów elektrycznych, przyczyniają się do zrównoważonego rozwoju przemysłu, zmniejszając zużycie energii i materiałów oraz ograniczając negatywny wpływ na środowisko.
Innowacyjne systemy chłodzenia i smarowania narzędzi
Rozwój nowoczesnych systemów chłodzenia i smarowania narzędzi skrawających ma kluczowe znaczenie dla ekologizacji maszyn CNC. Technologie takie jak systemy MQL (Minimum Quantity Lubrication) oraz chłodzenie kriogeniczne pozwalają znacznie ograniczyć zużycie tradycyjnych płynów chłodząco-smarujących, a tym samym zmniejszyć ilość niebezpiecznych odpadów dla środowiska.
Systemy MQL wykorzystują jedynie niewielką ilość oleju, która jest efektywnie rozpylana na ostrze narzędzia, zapewniając odpowiednie smarowanie i chłodzenie bez konieczności stosowania dużej ilości cieczy. Z kolei chłodzenie kriogeniczne, wykorzystujące ciekły azot, umożliwia uzyskanie bardzo niskich temperatur w strefie skrawania, znacząco poprawiając wydajność i trwałość narzędzi.
Kolejnym krokiem w kierunku zrównoważonej produkcji jest stosowanie biodegradowalnych olejów i emulsji jako środków smarno-chłodzących. Rozwiązania te, w połączeniu z zaawansowanymi systemami kontroli i monitorowania procesów, pozwalają na znaczne ograniczenie negatywnego wpływu obróbki skrawaniem na środowisko naturalne.
Technologia | Korzyści | Zastosowanie |
---|---|---|
Systemy MQL | Zredukowane zużycie płynów, mniejsza emisja odpadów | Obróbka różnych materiałów, w tym metali |
Chłodzenie kriogeniczne | Wysoka wydajność i trwałość narzędzi, precyzja obróbki | Obróbka trudnoobrabialnych stopów, metali i kompozytów |
Płyny chłodząco-smarujące biodegradowalne | Minimalizacja negatywnego wpływu na środowisko | Zastosowania ogólne w obróbce skrawaniem |
Innowacyjne technologie chłodzenia i smarowania narzędzi CNC odgrywają kluczową rolę w ekologizacji nowoczesnych procesów produkcyjnych, przyczyniając się do zmniejszenia zużycia zasobów i ograniczenia negatywnego wpływu na środowisko.
Monitorowanie stanu maszyny i narzędzia
Zaawansowane technologie monitorowania stanu maszyn pozwalają znacząco poprawić ciągłość działania oraz przedłużyć żywotność urządzeń. Predykcyjna diagnostyka, wykorzystująca zaawansowane algorytmy analityki danych, prowadzi do redukcji nieplanowanych przestojów w produkcji.
Monitorowanie stanu maszyn przyczynia się do realizacji celów biznesowych poprzez zwiększenie niezawodności operacyjnej i satysfakcji klientów. Różnorodne metody monitorowania obejmują inspekcje wizualne, analizę drgań, termografię oraz ciągły monitoring online.
Analiza drgań pomaga wykrywać nieprawidłowości w pracy maszyny, takie jak potencjalne problemy z łożyskami lub wirnikami. Z kolei termografia identyfikuje nadmierne wzrosty temperatur, zazwyczaj wynikające z przegrzewania się komponentów. Ciągły monitoring online polega na stałym śledzeniu parametrów maszyny, jak temperatura czy poziom oleju, aby natychmiast reagować na odchylenia.
Wdrażanie monitorowania stanu maszyn wymaga odpowiedniego doboru technologii i narzędzi dostosowanych do konkretnych typów urządzeń oraz środowiska pracy. Kluczowe jest również przeszkolenie personelu odpowiedzialnego za monitorowanie i interpretację danych.
Firma Balluff, będąca liderem w zakresie rozwiązań do monitorowania stanu maszyn, oferuje szeroką gamę produktów, takich jak czujniki drgań, czujniki temperatury, czujniki ciśnienia oraz systemy online.
Monitorowanie stanu maszyn ma kluczowe znaczenie dla utrzymania niezawodności operacyjnej, wydłużenia żywotności sprzętu, przewidywania potencjalnych awarii oraz planowania konserwacji z wyprzedzeniem w celu zwiększenia efektywności produkcji i redukcji kosztów.
Najnowsze narzędzia CNC na rynku
Producenci maszyn CNC nieustannie pracują nad opracowywaniem nowszych rozwiązań, które pozwalają na zwiększenie wydajności pracy. Urządzenia wykorzystujące najnowsze technologie CNC powinny zainteresować szczególnie tych, którym zależy na zoptymalizowaniu procesu cięcia, przyspieszeniu realizacji zleceń i maksymalizacji zysków.
Prognozy rozwoju branży narzędzi do obróbki metali wskazują na rosnące zapotrzebowanie na wysokowydajne narzędzia skrawające, zwłaszcza do obróbki stopów aluminium w przemyśle lotniczym i samochodowym. Dynamiczny rozwój maszyn CNC oraz technologii mikroobróbki sprawia, że producenci poszukują coraz efektywniejszych rozwiązań, w tym narzędzi do obróbki z wysokimi posuwami.
Obecnie, narzędzia skrawające wykonuje się głównie z węglika spiekanego HM i stali szybkotnącej HSS. Coraz popularniejsze stają się także narzędzia z materiałów supertwardych, takich jak diament polikrystaliczny PCD i azotek boru CBN. Trendy w produkcji narzędzi obejmują rosnące zapotrzebowanie na narzędzia precyzyjne, dedykowane określonym operacjom, oraz na narzędzia wielofunkcyjne, w związku z potrzebą obróbki elementów o skomplikowanych kształtach.
Przykładowo, najnowsze maszyny CNC wyposażone są w:
- Moc wrzeciona wynoszącą 9 kW
- Napędy serwonapędów Leadshine o mocy 1500W
- Stół roboczy o wymiarach 2100×4200 mm
- Oś Z o wysokości 300 mm
- Dokładność re-pozycjonowania na poziomie 0,01 mm
- Wagę 3350 kg
- Zasilanie 400 V oraz sprężone powietrze min. 8 bar
- Opcjonalną pompę próżniową o mocy 2×7,5 kW
- 8-pozycyjny liniowy magazyn narzędzi
- Oprogramowanie CAD/CAM z importem plików z Corela, Autocada i inne funkcje
- Wymiary maszyny 5070 x 2870 x 1900 mm
Takie rozwiązania pozwalają na zwiększenie wydajności i konkurencyjność rynku maszyn CNC, oferując nowe możliwości w zakresie przyszłości obróbki skrawaniem.
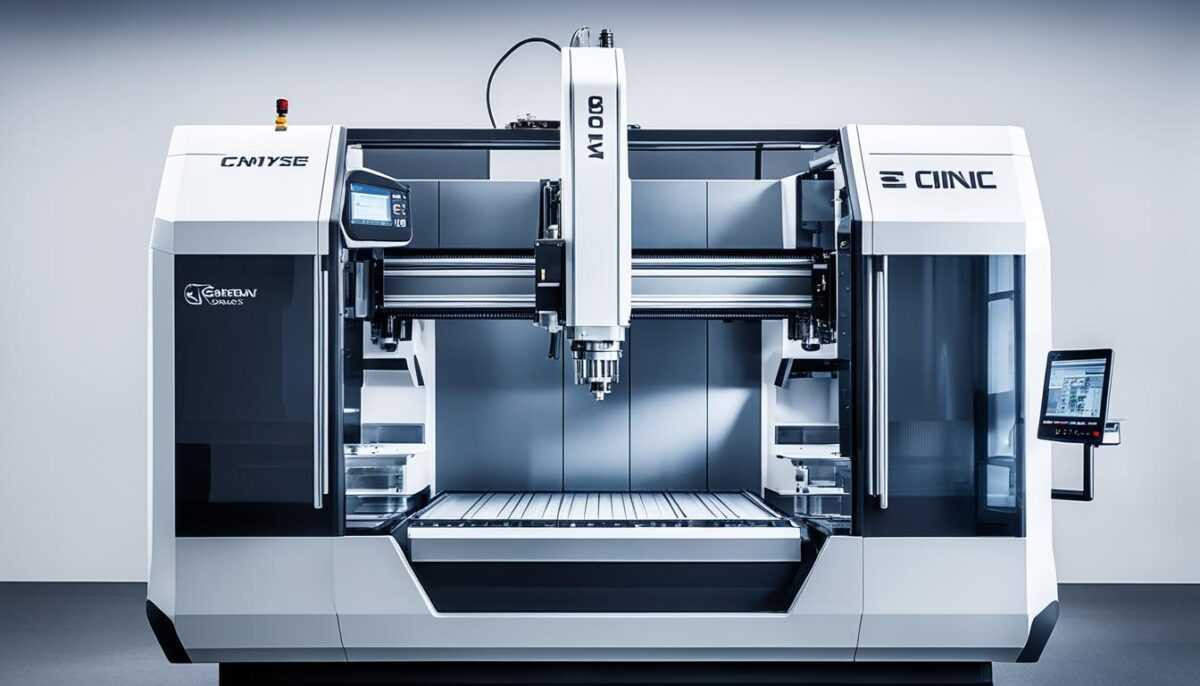
„Dynamiczny rozwój technologii sprawia, że producenci poszukują coraz efektywniejszych rozwiązań w zakresie narzędzi skrawających.”
Wniosek
Rynek maszyn CNC stale się rozwija, oferując coraz doskonalsze rozwiązania w zakresie obróbki skrawaniem. Innowacje te obejmują zarówno oprogramowanie, jak i sprzęt, umożliwiając producentom zwiększenie precyzji, efektywności oraz automatyzacji procesów produkcyjnych. Nowoczesne maszyny CNC są wyposażone w zaawansowane systemy sterowania, zdolne do samodzielnej optymalizacji parametrów cięcia, co przekłada się na oszczędność czasu i materiałów.
Dodatkowo, integracja z technologiami Przemysłu 4.0 otwiera drogę do inteligentnej produkcji, gdzie maszyny komunikują się między sobą i z operatorami w czasie rzeczywistym. Wszystko to sprawia, że branża obróbki skrawaniem dynamicznie się rozwija, a inwestycje w najnowsze technologie CNC stają się kluczowe dla utrzymania konkurencyjności na globalnym rynku.
Podsumowując, ciągły postęp w dziedzinie maszyn CNC i obróbki skrawaniem zapewnia producentom narzędzia, które pozwalają im zwiększyć wydajność, jakość i elastyczność procesów produkcyjnych. Firmy chcące pozostać konkurencyjne muszą ściśle śledzić najnowsze trendy CNC i inwestować w najnowocześniejsze rozwiązania z tej dziedziny.
FAQ
Jakie są najnowsze innowacje w technologiach CNC?
Najnowsze maszyny CNC są wyposażone w zaawansowane systemy sterowania, wykorzystujące sztuczną inteligencję i uczenie maszynowe do optymalizacji procesów skrawania. Ponadto, technologie IoT umożliwiają zdalny monitoring i kontrolę procesów produkcyjnych. Nowoczesne centra obróbcze cechują się także wysoką energooszczędnością i zrównoważonym podejściem do środowiska.
Jak nowe technologie wpływają na precyzję i efektywność obróbki skrawaniem?
Zaawansowane systemy sterowania pozwalają na dokładne przetwarzanie danych i realizację skomplikowanych operacji z wysoką powtarzalnością. Zastosowanie AI i ML umożliwia samoadaptację parametrów cięcia do zmiennych warunków, wydłużając żywotność narzędzi i poprawiając jakość wyrobów. Integracja z systemami CAD/CAM oraz symulacje 3D ułatwiają planowanie i optymalizację procesów produkcyjnych.
Jakie nowe materiały i systemy chłodzenia wykorzystywane są w nowoczesnych maszynach CNC?
Producenci maszyn CNC wdrażają zaawansowane systemy chłodzenia i smarowania narzędzi, takie jak technologia MQL lub chłodzenie kriogeniczne. Przyczynia się to do zwiększenia wydajności pracy, trwałości narzędzi oraz ograniczenia zużycia środków chłodząco-smarujących. Ponadto, nowe materiały i powłoki narzędzi skrawających umożliwiają pracę przy wyższych prędkościach cięcia.
W jaki sposób integracja IoT wpływa na monitorowanie i kontrolę maszyn CNC?
Dzięki integracji technologii bezprzewodowych i Internetu Rzeczy, nowoczesne maszyny CNC umożliwiają zdalny monitoring i kontrolę procesów produkcyjnych. Operatorzy mogą śledzić stan urządzeń na bieżąco, co pozwala na szybką reakcję w przypadku nieprawidłowości. Dodatkowo, zdalna diagnostyka i serwisowanie przyczyniają się do ograniczenia przestojów w produkcji.
Jakie są najnowsze trendy w interfejsach użytkownika i symulacjach cyfrowych w maszynach CNC?
Współczesne systemy sterowania CNC są wyposażone w zaawansowane, intuicyjne interfejsy użytkownika, które ułatwiają obsługę maszyn nawet dla mniej doświadczonych operatorów. Graficzne interfejsy użytkownika, wspomaganie decyzji przez system oraz symulacje cyfrowe pozwalają na szybsze uruchamianie nowych programów obróbczych i skracają czas potrzebny na szkolenie personelu.
Jak technologie adaptacyjnego sterowania wpływają na jakość obróbki skrawaniem?
Systemy adaptacyjnego sterowania procesami skrawania reagują na zmienne warunki obróbki w czasie rzeczywistym. Są one w stanie kompensować wpływ zużycia narzędzia czy zmian temperatury materiału obrabianego, co zapewnia stałą jakość produktu końcowego bez konieczności ciągłej interwencji operatora.
Jakie rozwiązania ekologiczne są stosowane w nowoczesnych maszynach CNC?
Producenci maszyn CNC wprowadzają coraz więcej rozwiązań ekologicznych, takich jak systemy MQL (Minimum Quantity Lubrication) lub chłodzenie kriogeniczne, które ograniczają zużycie płynów chłodząco-smarujących. Ponadto, wykorzystanie napędów elektrycznych o wysokiej sprawności energetycznej oraz optymalizacja procesów cięcia pod kątem redukcji odpadów przyczyniają się do zwiększenia zrównoważenia produkcji.
Jak systemy monitorowania stanu maszyny i narzędzia wpływają na wydajność i trwałość obrabiarek CNC?
Wprowadzenie technologii monitorowania stanu maszyny i narzędzia umożliwia przedłużenie ich żywotności, a także zapobieganie awariom i nieplanowanym przestojom. Systemy te zbierają dane dotyczące pracy maszyny, które następnie są analizowane w celu optymalizacji procesów produkcyjnych pod kątem zużycia energii oraz minimalizacji odpadów.