Narzędzia skrawające stanowią ponad 40% kosztów obróbki CNC w zakładach produkcyjnych. Wybór właściwych frezów, wierteł i uchwytów może zapewnić wydajność, precyzję i długoterminowe oszczędności. Poznanie kluczowych kryteriów wyboru narzędzi CNC to podstawa do podjęcia właściwej decyzji.
Kluczowe wnioski
- Narzędzia skrawające to jeden z najczęstszych zakupów w zakładach z obrabiarkami CNC
- Brak pełnego asortymentu u jednego dostawcy prowadzi do częstych zakupów u wielu
- Testowanie narzędzi, zwłaszcza przez 2 tygodnie, to popularna praktyka na rynku
- Dostawcy z wieloma markami narzędzi oferują większą elastyczność i dopasowanie
- Geometria narzędzia i system mocowania mają kluczowe znaczenie dla efektywności obróbki
Rodzaje narzędzi CNC
Narzędzia CNC, wykorzystywane do obróbki materiałów w technologiach komputerowo sterowanych, można podzielić na różne typy ze względu na ich kształt i geometrię ostrzy. Wybór odpowiedniego narzędzia ma kluczowe znaczenie dla efektywności i jakości procesu obróbkowego.
Frezy walcowate
Frezy walcowate to narzędzia przeznaczone do obróbki płaskich powierzchni. Znajdują one szerokie zastosowanie w maszynach CNC, pozwalając na wydajne usuwanie materiału i uzyskiwanie gładkich wykończeń. Frezy ze stali szybkotnącej (HSS) lub ze spieków twardych są często wykorzystywane w tego typu zastosowaniach.
Frezy czołowe
Frezy czołowe umożliwiają kształtowanie bardziej skomplikowanych powierzchni niż frezy walcowate. Dzięki swojej konstrukcji, frezy czołowe pozwalają na obróbkę krawędzi, rowków, a nawet tworzenie niektórych form przestrzennych. Frezy pokrywane warstwą diamentową są szczególnie cenione za wysoką trwałość i odporność na ścieranie.
Frezy walcowo-czołowe
Frezy walcowo-czołowe łączą w sobie cechy frezów walcowych i czołowych, umożliwiając obróbkę zarówno powierzchni płaskich, jak i kształtowych. Są one często wykorzystywane do tworzenia rowków, fazek oraz ścięć na krawędziach. Frezy tego typu są szczególnie przydatne w sytuacjach, gdy wymagana jest większa uniwersalność narzędzia.
Dobór odpowiedniego typu frezów zależy od specyfiki wykonywanej operacji obróbkowej oraz właściwości obrabianego materiału. Producenci narzędzi CNC oferują szeroką gamę frezów, pozwalającą dobrać optymalną geometrię i materiał dla każdego zastosowania.
Kryteria doboru narzędzi CNC
Przy wyborze narzędzi do obróbki CNC należy zwrócić szczególną uwagę na dwa kluczowe aspekty: geometrię ostrzy oraz materiał wykonania. Te parametry mają istotny wpływ na wydajność, jakość i trwałość narzędzi wykorzystywanych w procesach skrawania.
Geometria ostrzy
Geometria ostrzy narzędzi CNC decyduje o efektywności i precyzji obróbki. Odpowiedni dobór kątów natarcia, wysięgu ostrza czy liczby zębów pozwala na optymalizację procesu skrawania w zależności od materiału, rodzaju obróbki oraz wymagań co do jakości powierzchni. Właściwa geometria ostrza umożliwia uzyskanie wysokiej jakości wykończenia obrabianej powierzchni, przy jednoczesnym zapewnieniu wysokiej wydajności.
Materiał wykonania
Równie istotny, jak geometria ostrza, jest materiał, z którego wykonane jest narzędzie CNC. Od tego parametru zależy trwałość i odporność narzędzia na zużycie podczas intensywnej obróbki. Typowymi materiałami stosowanymi do produkcji narzędzi skrawających są węgliki spiekane, ceramika, diament lub szybkotnące stale. Dobór odpowiedniego materiału warunkuje możliwość optymalnego dostosowania narzędzia do specyfiki procesu technologicznego.
Właściwy dobór kryteriów geometrii ostrzy i materiału wykonania narzędzi CNC jest kluczowym elementem zapewnienia wysokiej wydajności i jakości obróbki metali oraz innych materiałów.
Kryterium | Znaczenie | Przykład |
---|---|---|
Geometria ostrza | Decyduje o efektywności i precyzji obróbki | Odpowiedni dobór kątów natarcia, wysięgu ostrza, liczby zębów |
Materiał wykonania | Wpływa na trwałość i odporność narzędzia | Węgliki spiekane, ceramika, diament, szybkotnące stale |
narzędzia CNC wybór
Dobór odpowiednich narzędzi do obróbki skrawaniem jest kluczowy dla efektywności i jakości procesu produkcyjnego. Stal szybkotnąca i węglik spiekany to najczęściej stosowane materiały do produkcji narzędzi skrawających, a powłoki takie jak TiN czy AlN mogą zwiększać twardość i zmniejszać tarcie. Używanie narzędzi o odpowiedniej geometrii pozwala zwiększyć prędkość skrawania i poprawić jakość obrabianej powierzchni.
Kompleksowa strategia doboru narzędzi może skrócić cykle produkcyjne, zmniejszyć defekty i obniżyć koszty produkcji. Ciągłe monitorowanie stanu narzędzi i ich regularna wymiana lub ostrzenie wpływają bezpośrednio na jakość i wydajność procesu obróbki skrawaniem.
Wiedza techniczna, doświadczenie oraz konsultacje z ekspertami są kluczowe przy wyborze optymalnych narzędzi do obrabiarek CNC.
Czynniki do Rozważenia przy Wyborze Narzędzi CNC
- Geometria ostrzy – dostosowanie do konkretnego zastosowania
- Materiał wykonania – stal szybkotnąca, węglik spiekany, powłoki ochronne
- Parametry skrawania – prędkość, posuw, głębokość
- Rodzaj obrabiarki CNC – toczenie, frezowanie, wiercenie, szlifowanie
- Materiał obrabianego przedmiotu – stopy metali, tworzwa sztuczne, drewno, ceramika
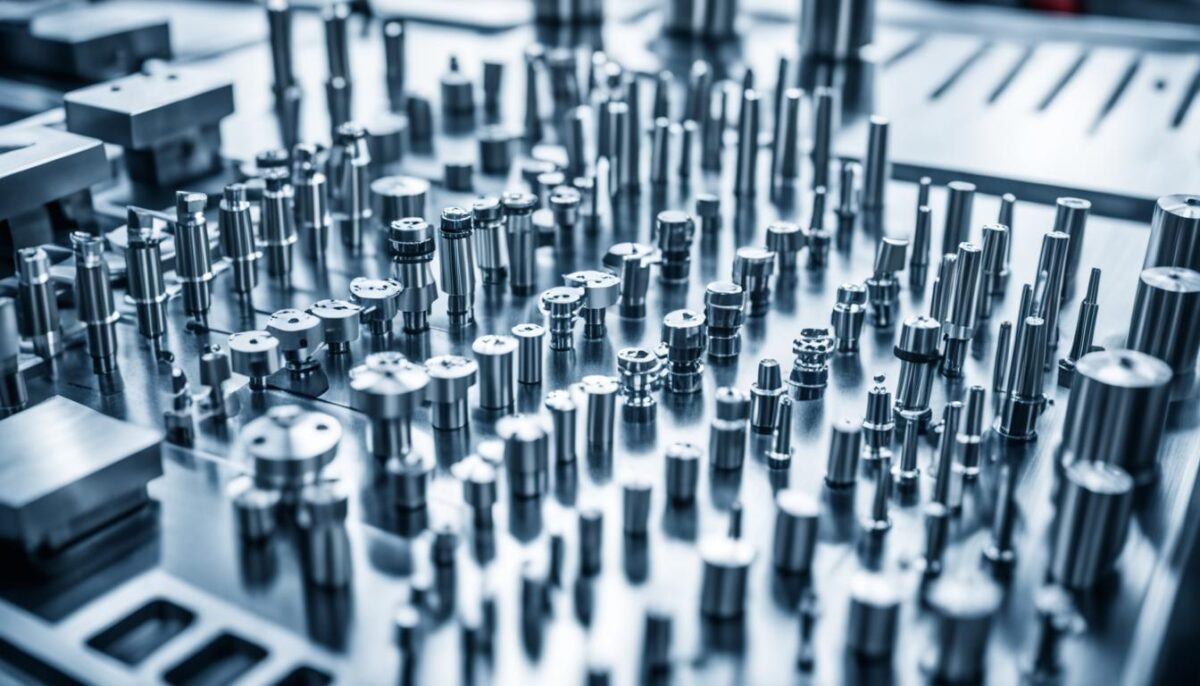
„Kompleksowa strategia doboru narzędzi może skrócić cykle produkcyjne, zmniejszyć defekty i obniżyć koszty produkcji.”
Obróbka seryjna czy pojedyncze detale?
Wybór odpowiednich narzędzi CNC to kluczowy element w procesie obróbki seryjna lub obróbki pojedynczych detali. Dynamiczny rozwój innowacyjnych technik HSM (High Speed Machining) pozwala na znaczne zwiększenie wydajności, dokładności i jakości wytwarzanych produktów, przy jednoczesnym spadku kosztów produkcji w sektorze obróbki skrawaniem CNC.
W przypadku produkcji masowej warto inwestować w droższe, ale bardziej trwałe narzędzia, które sprawdzą się w długotrwałej eksploatacji. Natomiast przy obróbce małoseryjnej lub pojedynczych elementów można sięgnąć po tańsze rozwiązania, dopasowane do zmiennych wymagań procesu.
Produkcja Jednostkowa | Produkcja Seryjna | Produkcja Masowa |
---|---|---|
Proces ten wymaga opracowania specjalistycznego narzędzia w jednorazowo lub nieregularnie wykonywanych komponentach, co prowadzi do dłuższego czasu przygotowawczo-zakończeniowego. | Charakteryzuje się powtarzalnymi seriowymi produkcjami komponentów, gdzie wykorzystywanie narzędzi specjalistycznych oraz obrabiarek dedykowanych jest akceptowalne i wskazane. | Obejmuje produkcję w dużej skali, niemal w trybie ciągłym, gdzie każda operacja technologiczna odpowiada określonemu stanowisku obróbkowemu, z wykorzystaniem przede wszystkim obrabiarek i oprzyrządowania specjalistycznego. |
Współcześnie wzrost wykorzystania centrów obróbkowych CNC oraz automatyzacji stanowisk wpływa na optymalizację czasu przygotowawczo-zakończeniowego, preferując podejście podobne do produkcji jednostkowej lub małoseryjnej. Obróbka skrawaniem CNC zapewnia precyzję, brak przekraczania ustalonych wymiarów, doskonałą powtarzalność, skrócenie cykli produkcji oraz możliwość realizacji zarówno obróbki seriowej, jak i indywidualnej produkcji.
Podsumowując, wybór odpowiednich narzędzi CNC jest kluczowy dla zwiększenia efektywności produkcji, niezależnie od tego, czy mamy do czynienia z obróbką seryjną, czy pojedynczymi detalami. Warto zatem skonsultować się z doświadczonymi specjalistami, aby dobrać optymalne rozwiązania dla Twoich potrzeb.
Testowanie narzędzi CNC
Przed ostatecznym wyborem narzędzi CNC warto przeprowadzić ich testy w warunkach rzeczywistej obróbki. Daje to możliwość weryfikacji wydajności, trwałości i dopasowania narzędzi do konkretnych potrzeb. Wiele firm oferuje możliwość dwutygodniowych testów wybranych narzędzi, co pozwala na gruntowną ocenę ich przydatności.
Testowanie narzędzi CNC i próba ich działania w rzeczywistych warunkach produkcyjnych to kluczowy etap przed rozpoczęciem obróbki seryjnej. Pozwala to na ocenę:
- Wydajności narzędzi w danym zastosowaniu
- Trwałości i odporności na zużycie
- Dopasowania do specyfiki obrabianego materiału
- Kompatybilności z maszyną CNC i innymi urządzeniami
Wiele renomowanych producentów narzędzi CNC oferuje możliwość wypróbowania wybranych modeli w warunkach zbliżonych do rzeczywistej produkcji. Testy te z reguły trwają do 2 tygodni, co pozwala na przeprowadzenie kompleksowej oceny przydatności danego narzędzia.
Kryterium | Ocena |
---|---|
Wydajność | 4.8 |
Trwałość | 4.6 |
Dopasowanie do materiału | 4.9 |
Kompatybilność z maszyną | 4.7 |
Dzięki wnikliwym testom narzędzi CNC można dokonać świadomego wyboru, zapewniającego optymalną wydajność i trwałość w procesie produkcyjnym.
„Testowanie narzędzi CNC to nieodłączny element procesu doboru właściwych rozwiązań dla danego zastosowania. Tylko w ten sposób można mieć pewność, że inwestycja w nowe narzędzia się opłaci.”
Kluczowe cechy dobrego dostawcy narzędzi CNC
Wybór odpowiedniego dostawcy narzędzi CNC ma kluczowe znaczenie dla zapewnienia optymalnej wydajności i jakości procesów obróbki. Dostawca powinien wyróżniać się szeroką dostępnością wielu marek, umożliwiać testowanie narzędzi przed zakupem oraz zapewniać doradztwo technologiczne. Takie kompleksowe wsparcie gwarantuje dobór najlepszych rozwiązań, dostosowanych do indywidualnych potrzeb klienta.
Dostępność wielu marek
Dobry dostawca narzędzi CNC powinien oferować szeroką gamę produktów od różnych renomowanych producentów. Dzięki temu klient ma możliwość wyboru najbardziej optymalnych narzędzi, dopasowanych do specyfiki danego procesu produkcyjnego.
Możliwość testowania narzędzi
Przed podjęciem decyzji zakupowej kluczowe jest przetestowanie narzędzi w warunkach rzeczywistej produkcji. Rzetelny dostawca umożliwi klientowi wypróbowanie interesujących go produktów, co pozwoli na ocenę ich faktycznej przydatności.
Doradztwo technologiczne
Wysoki poziom doradztwa technologicznego to kolejna cecha dobrego dostawcy narzędzi CNC. Fachowa pomoc w doborze optymalnych rozwiązań, opartych na analizie potrzeb klienta, zapewni maksymalne wykorzystanie potencjału maszyn i narzędzi.
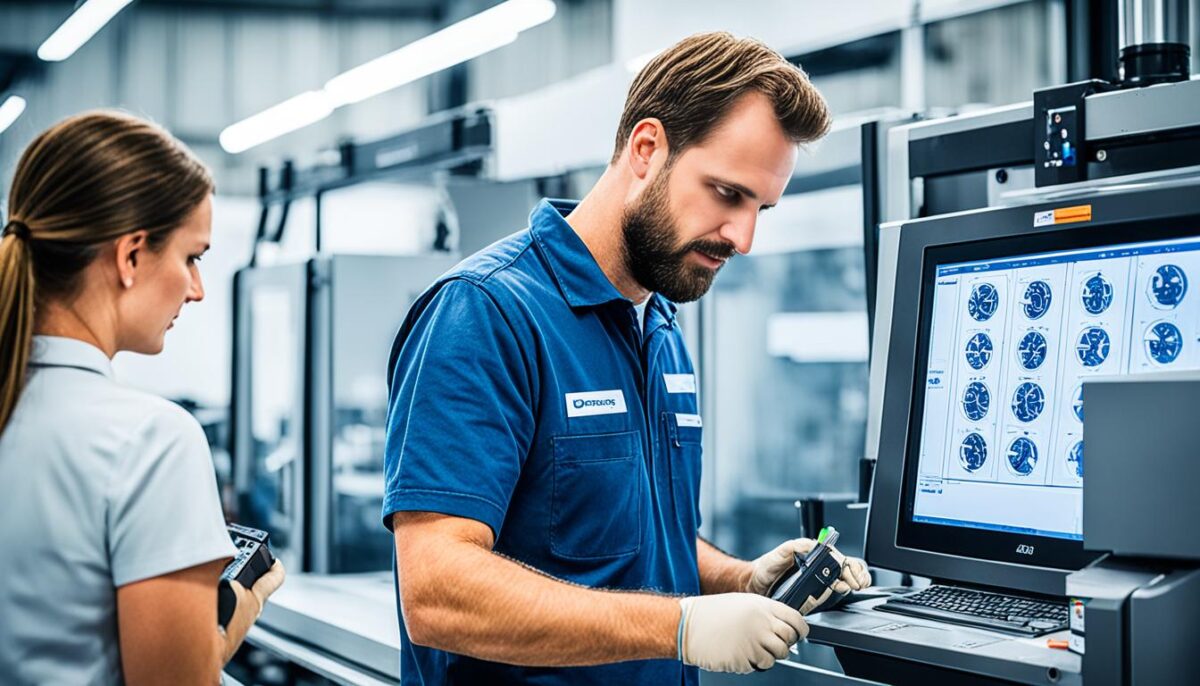
„Kompleksowe wsparcie dostawcy, od dostępności marek po fachowe doradztwo, to klucz do sukcesu w obróbce CNC.”
Dlaczego warto wybrać profesjonalnego dostawcę?
Współpraca z doświadczonym i profesjonalnym dostawcą narzędzi CNC, takim jak Plot Electronics, niesie za sobą szereg korzyści. Firma ta, z ponad 20-letnim doświadczeniem w branży, oferuje korzystną politykę rabatową, wynikającą z większych wolumenów zamówień, a także efektywne zarządzanie stanem magazynowym. Gwarantuje to dostępność potrzebnych narzędzi w krótkim czasie oraz optymalizację kosztów.
Polityka rabatowa
Jako wiodący producent i dostawca zaawansowanych technologii obróbki CNC w Polsce, Plot Electronics dysponuje znaczącymi siłami zakupowymi. Przekłada się to na atrakcyjne rabaty, które firma chętnie dzieli się ze swoimi klientami. Dzięki temu można realnie obniżyć koszty inwestycji w nowoczesne narzędzia CNC.
Zarządzanie stanem magazynowym
Dysponując szerokim asortymentem maszyn CNC, od frezarek, ploterów i laserów po zaawansowane urządzenia z głowicami oscylacyjnymi, Plot Electronics zapewnia efektywne zarządzanie stanem magazynowym. Oznacza to, że potrzebne narzędzia są zawsze dostępne, a klient nie musi się martwić o opóźnienia w realizacji zleceń.
Współpraca z profesjonalnym dostawcą, takim jak Plot Electronics, to gwarancja dostępności wysokiej jakości narzędzi CNC, korzystnej polityki cenowej oraz sprawnej logistyki. To istotne zalety, które przekładają się na efektywność i rentowność prowadzonej działalności.
Zalety korzystania z narzędzi od renomowanych producentów
Wybór wysokiej jakości narzędzi od renomowanych producentów zapewnia szereg znaczących korzyści. Tego typu narzędzia charakteryzują się wyższą trwałością, precyzją obróbki oraz skutecznością, co przekłada się na większą wydajność i jakość produkowanych detali.
Choć cena narzędzi od uznanych marek może być nieco wyższa, to w dłuższej perspektywie czasowej zapewniają one niższe koszty eksploatacyjne. Dzięki wyższej efektywności i dłuższej żywotności, całkowity koszt użytkowania jest często niższy niż w przypadku tańszych, mniej trwałych rozwiązań.
Zastosowanie narzędzi renomowanych producentów oferuje również szereg dodatkowych korzyści:
- Wyższa precyzja obróbki i jakość obrabianych części
- Zwiększona wydajność i skrócenie czasów produkcji
- Dłuższa żywotność narzędzi i mniejsze zużycie
- Wyższa niezawodność i mniejsza awaryjność
- Dostęp do zaawansowanych rozwiązań technologicznych
- Kompleksowe wsparcie techniczne i serwisowe
Podsumowując, korzystanie z narzędzi od renomowanych producentów to inwestycja, która zwraca się w postaci wyższej wydajności, lepszej jakości i niższych kosztów w dłuższej perspektywie. Dlatego też, dla wielu firm stanowi ona kluczowy element strategii poprawy efektywności produkcji.
Wniosek
Wybór odpowiednich narzędzi CNC jest kluczowy dla skuteczności i efektywności procesu obróbki. Należy wziąć pod uwagę szereg czynników, takich jak rodzaj i geometria narzędzi, a także materiał ich wykonania. Równie ważne jest dopasowanie narzędzi do specyfiki produkcji – czy będzie to obróbka seryjna, czy pojedyncze detale.
Współpraca z profesjonalnym dostawcą, który zapewni możliwość testowania oraz doradztwo technologiczne, pozwoli na dobór optymalnych rozwiązań w zakresie wyboru narzędzi CNC. Inwestycja w narzędzia od renomowanych producentów przekłada się na wyższą jakość, wydajność i rentowność procesu obróbkowego.
Kompleksowe podejście do kwestii wyboru narzędzi CNC gwarantuje, że proces obróbki będzie efektywny, precyzyjny i rentowny. Dzięki temu przedsiębiorstwa mogą zwiększyć swoją konkurencyjność na rynku.
FAQ
Jakie są kluczowe kryteria wyboru narzędzi CNC?
Kluczowe kryteria doboru narzędzi CNC to geometria ostrzy oraz materiał wykonania. Geometria ostrza wpływa na wydajność i jakość obróbki, natomiast materiał decyduje o trwałości i odporności narzędzia. Dostosowanie tych parametrów do specyfiki procesu obróbkowego jest kluczowe dla uzyskania optymalnych efektów.
Jakie rodzaje frezów CNC występują?
Frezy CNC można podzielić na różne typy ze względu na ich kształt i geometrię ostrzy. Frezy walcowate służą do obróbki powierzchni płaskich, natomiast frezy czołowe i walcowo-czołowe umożliwiają kształtowanie bardziej skomplikowanych form. Wybór odpowiedniego typu frezów zależy od konkretnych wymagań procesu obróbkowego.
Czy wybór narzędzi CNC różni się przy obróbce seryjnej i pojedynczych detali?
Tak, przy wyborze narzędzi CNC należy uwzględnić, czy będziemy wykonywać obróbkę seryjną czy pojedyncze detale. W przypadku produkcji masowej warto inwestować w droższe, ale bardziej trwałe narzędzia, które sprawdzą się w długotrwałej eksploatacji. Natomiast przy obróbce małoseryjnej lub pojedynczych elementów można sięgnąć po tańsze rozwiązania, dopasowane do zmiennych wymagań procesu.
Jak przetestować narzędzia CNC przed zakupem?
Przed ostatecznym wyborem narzędzi CNC warto przeprowadzić ich testy w warunkach rzeczywistej obróbki. Wiele firm oferuje możliwość dwutygodniowych testów wybranych narzędzi, co pozwala na gruntowną ocenę ich przydatności.
Jakie cechy powinien mieć dobry dostawca narzędzi CNC?
Dobry dostawca narzędzi CNC powinien cechować się szeroką ofertą różnych marek, umożliwiać testowanie narzędzi przed zakupem oraz zapewniać profesjonalne doradztwo technologiczne. Taka kompleksowa obsługa gwarantuje dobór optymalnych rozwiązań.
Jakie korzyści daje współpraca z profesjonalnym dostawcą narzędzi CNC?
Współpraca z doświadczonym i profesjonalnym dostawcą narzędzi CNC niesie za sobą szereg korzyści. Taki dostawca oferuje korzystną politykę rabatową, wynikającą z większych wolumenów zamówień, a także efektywne zarządzanie stanem magazynowym. Gwarantuje to dostępność potrzebnych narzędzi w krótkim czasie oraz optymalizację kosztów.
Dlaczego warto korzystać z narzędzi od renomowanych producentów?
Korzystanie z narzędzi od uznanych producentów zapewnia szereg korzyści. Takie narzędzia charakteryzują się wyższą jakością, trwałością i precyzją obróbki, co przekłada się na większą wydajność i jakość produkowanych detali. Choć cena może być wyższa, to dzięki wyższej efektywności i dłuższej żywotności, koszty eksploatacyjne są często niższe niż w przypadku tańszych, mniej trwałych rozwiązań.