Nawet 700 amperów – taka jest moc regularnie przepływająca przez łuk spawalniczy podczas typowego procesu spawania. Choć spawanie jest z natury energochłonnym procesem, to istnieje wiele możliwości, aby zredukować jego wpływ na środowisko i ograniczyć zużycie energii. Firmy wdrażające ekologiczne techniki spawalnicze, takie jak spawanie TIGiem czy MIG/MAG, mogą zaobserwować znaczną redukcję emisji szkodliwych gazów oraz pyłów, co przyczynia się do poprawy stanu środowiska. Ponadto, wykorzystanie tych metodologii pozwala na znaczne zmniejszenie zużycia energii, co przekłada się na wymierne oszczędności finansowe dla przedsiębiorstw.
Kluczowe wnioski
- Zastosowanie nowoczesnych, energooszczędnych technologii spawalniczych pozwala na zmniejszenie zużycia energii, a co za tym idzie, redukcję kosztów
- Procesy spawania TIG i MIG/MAG charakteryzują się niższą emisją szkodliwych związków, poprawiając jakość powietrza w zakładach przemysłowych
- Automatyzacja procesu spawania MIG/MAG umożliwia zmniejszenie ilości odpadów produkcyjnych, co korzystnie wpływa na środowisko
- Wykorzystanie materiałów spawalniczych z recyklingu wspiera ideę zrównoważonego rozwoju i zmniejsza obciążenie planety
- Inwestycje w technologie umożliwiające ponowne wykorzystanie odpadów spawalniczych przyczyniają się do ograniczenia wytwarzanych odpadów
Technologia inwertorowa zamiast starych spawarek analogowych
Spawanie to kluczowy proces w wielu gałęziach przemysłu, ale niestety też energochłonne. Tradycyjne, analogowe spawarki zużywają znacznie więcej energii niż nowocześniejsze, inwerterowe urządzenia spawalnicze. Urządzenia inwertorowe zużywają nawet o jedną trzecią mniej energii elektrycznej niż ich starsze, analogowe odpowiedniki.
Nowoczesne urządzenia inwertorowe zużywają mniej energii niż stare urządzenia analogowe
Wynika to z faktu, że w przypadku urządzeń inwertorowych energia pobierana jest faktycznie wykorzystywana do spawania, podczas gdy w starych, analogowych spawarkach znaczna część energii jest marnowana w postaci ciepła. Dzięki tej oszczędności zasilania, urządzenia inwertorowe przyczyniają się do zwiększenia energooszczędności w procesach spawania.
Mniejszy, lżejszy i bardziej mobilny design dzięki mniejszym transformatorom
Kolejną zaletą urządzeń inwertorowych jest ich mniejszy, lżejszy i bardziej mobilny design. Wynika to z zastosowania mniejszych transformatorów, w porównaniu do tradycyjnych spawarek analogowych. To czyni urządzenia inwertorowe łatwiejszymi w transporcie i obsłudze, co docenią zwłaszcza spawacze pracujący w różnych lokalizacjach.
Parametr | Spawarki analogowe | Urządzenia inwertorowe |
---|---|---|
Zużycie energii | Wysokie | Niskie (o 1/3 mniej) |
Waga | Duża | Mniejsza (dzięki mniejszym transformatorom) |
Mobilność | Niska | Wysoka |
Urządzenia inwertorowe nie są sobie równe
Chociaż wszystkie spawarki inwertorowe oferują znacznie większą efektywność energetyczną niż tradycyjne spawarki analogowe, to między poszczególnymi modelami inwertorów występują mierzalne różnice w oszczędności energii. Kluczową rolę w tym odgrywa funkcja korekcji współczynnika mocy, która pomaga zwiększyć sprawność energetyczną spawania.
Funkcja korekcji współczynnika mocy zwiększa efektywność energetyczną
Współczynnik mocy określa, jak sprawnie energia elektryczna jest wykorzystywana. Nowoczesne spawarki inwertorowe, wyposażone w funkcję korekcji współczynnika mocy, potrafią zminimalizować straty i doprowadzić do sytuacji, w której prawie cała pobierana energia jest przekazywana do procesu spawania. Transluje się to na znaczące oszczędności energii w porównaniu do starszych modeli.
Najnowsze urządzenia inwertorowe są bardziej energooszczędne od starszych modeli
Testy wykazały, że najnowocześniejsze spawarki inwertorowe zużywają o 255 kWh rocznie mniej energii niż nieco starsze modele. To ogromna różnica, która przekłada się na wymierne oszczędności dla użytkowników. Dlatego warto inwestować w najbardziej energooszczędne urządzenia inwertorowe, aby osiągać wysoką wydajność przy minimalnym zużyciu prądu.
Cyfryzacja zwiększa efektywność energetyczną
Oprócz rozwoju samego sprzętu spawalniczego, znaczące innowacje powstają również w połączeniu z oprogramowaniem. Cyfrowe innowacje stanowią podstawę dla nowych, bardziej wydajnych metod i procesów spawania, które przekładają się na zmniejszenie zużycia energii.
Przykładami są procesy CMT (Cold Metal Transfer) i PMC (Pulse Multi Control), które dzięki precyzyjnej regulacji i stabilnemu łukowi spawalniczemu minimalizują wypaczenie materiału podstawowego i zmniejszają ilość odrzutów, co wpływa na oszczędność energii.
„Według przeprowadzonego badania redakcyjnego, wśród obiektów objętych badaniem, około 58% wykorzystuje różne urządzenia do mechanizacji procesów spawania, 65% korzysta z robotów spawalniczych, a około 47% posiada stanowiska z robotami spawalniczymi w eksploatacji.”
Inwestując w automatyzację spawania, najważniejszymi czynnikami brane pod uwagę są cena zakupu (76%), jakość (65%) oraz parametry techniczne (59%). Respondenci doceniają również wsparcie techniczne od producenta/dostawcy (47%), markę producenta (41%) oraz okres gwarancji i zwrotu z inwestycji (29%).
Kluczowe parametry techniczne, które mają kluczowe znaczenie dla automatyzacji, to wydajność (82%), niezawodność (82%) oraz łatwość obsługi (76%). Istotne są również elastyczność zastosowań (47%), efektywność energetyczna (47%) oraz rozwiązania przyjazne dla środowiska (24%).
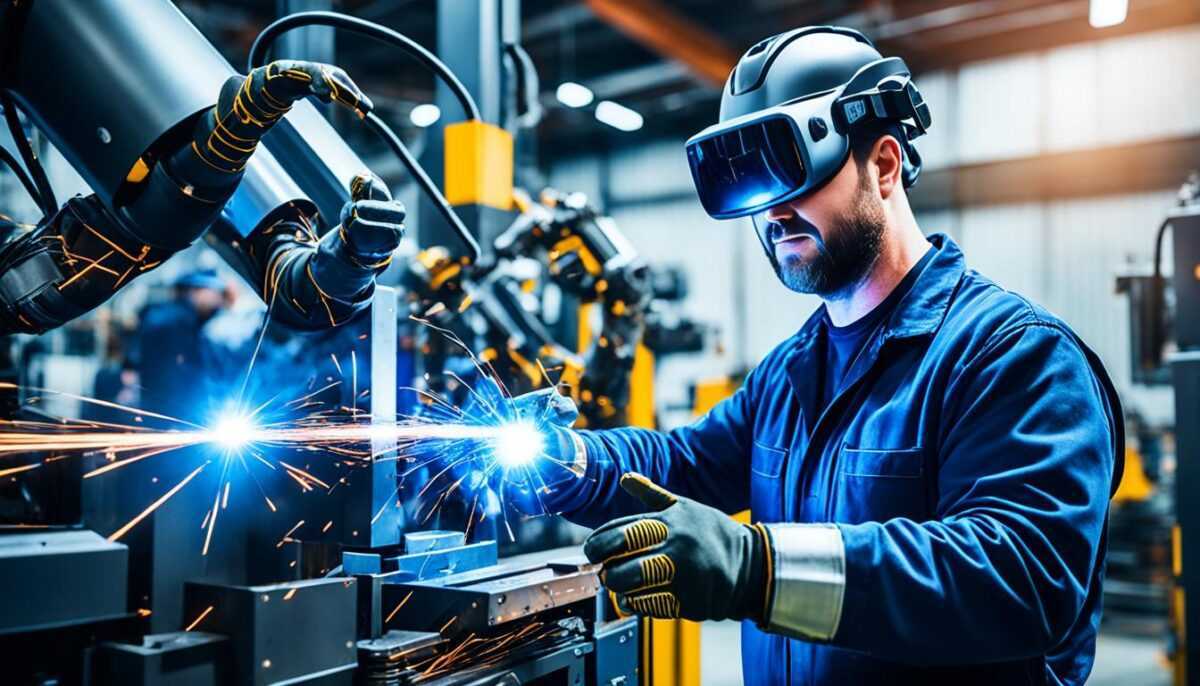
Nowoczesne roboty spawalnicze oferują zaawansowane funkcje, takie jak zwiększona pamięć, zdalne komunikowanie się za pomocą tabletów lub telefonów, zintegrowane okablowanie w ramieniu robota oraz możliwość łączenia ze źródłami spawalniczymi różnych renomowanych marek. Ich wszechstronność umożliwia montaż w standardowych pozycjach, na sufitach lub pod kątem, co ułatwia dostęp do wielu lokalizacji.
Nowoczesne procesy spawania = szybsze spawanie = mniejsze zużycie energii
Postęp w dziedzinie technologii spawalniczych otwiera nowe możliwości, które pozwalają na zwiększenie prędkości spawania, a tym samym na zmniejszenie zużycia energii podczas tego procesu. Nowoczesne procesy spawania, takie jak CMT (Cold Metal Transfer) i PMC (Pulse Multi Control), wyróżniają się wysoką wydajnością i stabilnością łuku, zapewniając jednocześnie zauważalne oszczędności energetyczne.
Proces CMT z precyzyjnie regulowanym doprowadzaniem prądu
Technologia CMT wykorzystuje precyzyjną kontrolę nad doprowadzaniem prądu do materiału, co pozwala uzyskać stabilny i energooszczędny łuk spawalniczy. W procesie tym, dzięki właściwemu dopasowaniu parametrów spawania, można znacząco zwiększyć prędkość spawania, co bezpośrednio przekłada się na mniejsze zużycie energii.
Pulse Multi Control (PMC) zapewnia wyższą prędkość spawania i mniejsze wprowadzanie energii
Kolejnym przykładem nowoczesnego, energooszczędnego procesu spawania jest PMC. Technologia ta, opierając się na zoptymalizowanym łuku pulsującym, pozwala uzyskać o 15-20% większą prędkość spawania przy niezmienionym lub nawet wyższym poziomie jakości spoiny. Przekłada się to na mniejsze wprowadzenie energii do materiału podstawowego, co skutkuje dalszymi oszczędnościami energetycznymi.
„Nowoczesne technologie spawalnicze, takie jak CMT i PMC, nie tylko poprawiają wydajność, ale również przyczyniają się do znacznych oszczędności energetycznych w porównaniu do tradycyjnych metod spawania.”
zmniejszenie zużycia energii spawanie
Dążenie do redukcji zużycia energii w spawaniu jest kluczowe dla osiągnięcia długoterminowej zrównoważoności przemysłu. Szczęśliwie, dzisiejsze nowoczesne technologie i procesy spawalnicze umożliwiają skuteczną optymalizację wydajności energetycznej, jednocześnie zapewniając wysoką jakość spoin. Spawanie staje się coraz bardziej ekologiczne i efektywne energetycznie.
Kluczowe czynniki, które przyczyniają się do zmniejszenia zużycia energii w spawaniu, obejmują:
- Zastosowanie nowych, energooszczędnych urządzeń inwertorowych zamiast starszych analogowych spawarek
- Wdrożenie nowoczesnych procesów spawania, takich jak CMT (Cold Metal Transfer) i Pulse Multi Control (PMC), które zapewniają wyższą prędkość i niższe dostarczanie energii
- Właściwa konfiguracja i obsługa sprzętu spawalniczego przez wykwalifikowanych spawaczy
- Optymalizacja chłodzenia i dopasowanie go do aktualnego zapotrzebowania na energię
- Zapewnienie stałego przepływu prądu i podawania drutu spawalniczego
- Prawidłowy dobór gazu osłonowego i ilości jego zużycia
Podsumowując, zmniejszenie zużycia energii podczas spawania oraz zwiększenie energoefektywności procesów spawalniczych to kluczowe cele, które mogą być osiągnięte dzięki kompleksowemu podejściu obejmującemu nowoczesne technologie, procesy i praktyki spawalnicze. Poprawa efektywności energetycznej w spawaniu to jeden z najważniejszych kroków w kierunku zrównoważonego rozwoju całego sektora.
Czynnik | Korzyść |
---|---|
Technologia inwertorowa | Około 4 kW mniejsze zużycie energii w porównaniu do konwencjonalnych spawarek |
Procesy CMT i PMC | Wyższa prędkość spawania i mniejsze dostarczanie energii |
Odpowiednia konfiguracja sprzętu | Optymalny przepływ prądu i drutu, precyzyjna osłona gazowa |
Chłodzenie dopasowane do zapotrzebowania | Wydłużenie żywotności urządzeń i poprawa efektywności energetycznej |
Połączenie nowoczesnych technologii spawalniczych, energooszczędnych procesów i właściwej obsługi sprzętu przez wykwalifikowanych spawaczy to klucz do osiągnięcia wysokiej wydajności energetycznej podczas spawania przy zachowaniu doskonałej jakości spoin.
Chłodzenie dostosowane do wydajności
Większość wysokowydajnych urządzeń MIG/MAG wykorzystuje chłodzenie płynowe w uchwycie spawalniczym. Niestety, nie zawsze jest to energooszczędne rozwiązanie. W wielu starszych modelach, płyn chłodzący krąży z tą samą prędkością, niezależnie od ilości energii dostarczanej do łuku spawalniczego. Nowoczesne urządzenia spawalnicze oferują jednak inny, znacznie bardziej efektywny sposób chłodzenia.
Chłodzenie dopasowane do aktualnego zapotrzebowania na energię
Chłodzenie dostosowane do wydajności oznacza, że wydajność układu chłodzenia jest powiązana ze zużyciem energii. Oznacza to, że używana jest tylko taka ilość energii, jaka jest potrzebna do uzyskania optymalnego rezultatu spawania, co pozwala uniknąć niepotrzebnego chłodzenia i tym samym zmniejszyć zużycie energii.
Funkcja | Korzyści |
---|---|
Chłodzenie dopasowane do wydajności |
|
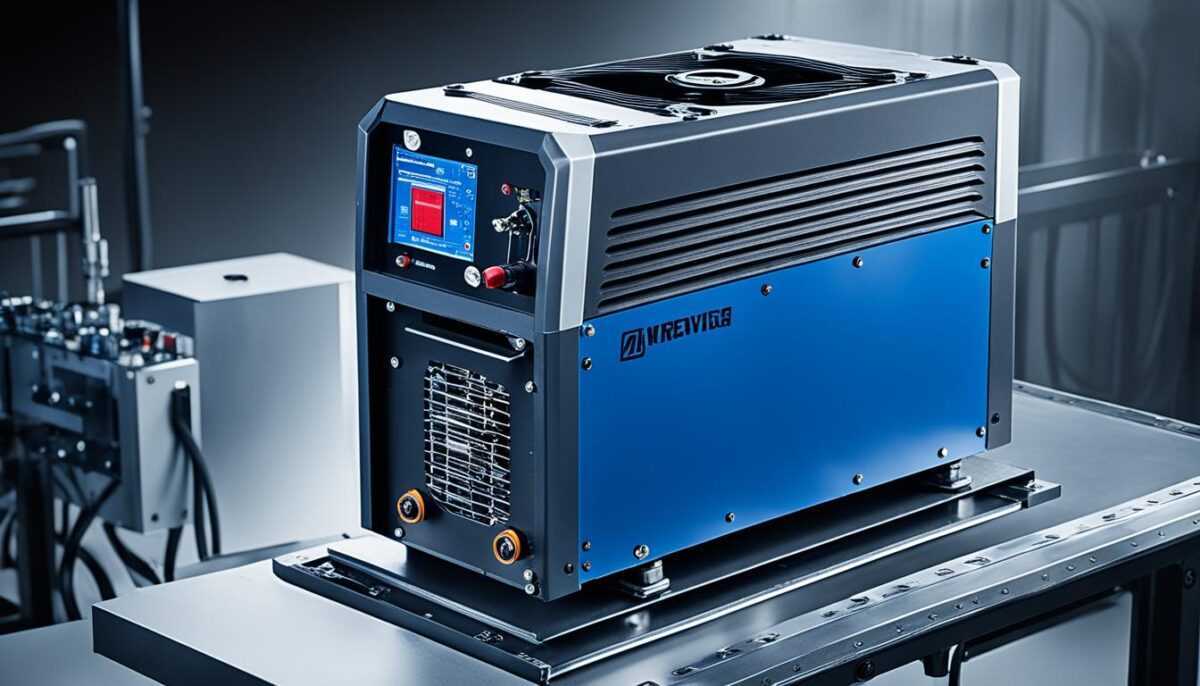
Nowoczesne urządzenia spawalnicze, takie jak spawarki z serii Migatronic Pi, wykorzystują zaawansowane funkcje chłodzenia, które automatycznie dostosowują wydajność układu chłodzenia do aktualnego zapotrzebowania na energię podczas spawania. Dzięki temu, chłodzenie urządzeń spawalniczych staje się bardziej energooszczędne, co przekłada się na znaczne oszczędności finansowe i ekologiczne dla firm.
Co mogą zrobić sami spawacze?
Spawacze mają istotny wpływ na zmniejszenie zużycia energii podczas spawania. Jednym z kluczowych działań, jakie mogą podjąć, jest wybór nowoczesnego i energooszczędnego urządzenia inwertorowego. Nowoczesne spawarki inwertorowe charakteryzują się znacznie niższym zużyciem energii w porównaniu do starszych modeli analogowych.
Ponadto, spawacze powinni zadbać o konfigurację nowoczesnych procesów spawania w swoich urządzeniach. Procesy takie jak CMT (Cold Metal Transfer) czy Pulse Multi Control (PMC) pozwalają na uzyskanie wyższej prędkości spawania i mniejszego wprowadzania energii, co przekłada się na oszczędność energii.
- Spawacze mogą dostosowywać parametry spawania, takie jak prąd i napięcie, do aktualnych potrzeb, unikając nadmiernego zużycia energii.
- Dbanie o regularne czyszczenie i konserwację sprzętu spawalniczego, w tym dysz gazowych i końcówek prądowych, wydłuża ich żywotność i poprawia efektywność energetyczną.
- Odpowiedni dobór i rozmieszczenie przewodów spawalniczych pozwala zminimalizować straty energii wynikające z oporów elektrycznych.
Podsumowując, działania spawaczy na rzecz oszczędności energii, takie jak wybór nowoczesnych i energooszczędnych urządzeń oraz właściwa konfiguracja procesów spawania, mogą w znacznym stopniu przyczynić się do ograniczenia zużycia energii w spawalnictwie.
Zapewnienie stałego przepływu prądu
Kluczowym elementem w spawaniu, który pozwala uniknąć powstawania odprysków, jest stabilny przepływ prądu. Aby to osiągnąć, ważne jest, aby prawidłowo połączyć uchwyt spawalniczy z systemem spawania oraz zapewnić dobre połączenie masy z materiałem, który jest spawany.
Ważne jest, aby miejsce zamocowania uchwytu spawalniczego i zacisku masy były oczyszczone i charakteryzowały się dobrą przewodnością elektryczną. Tylko wówczas prąd będzie mógł płynąć płynnie, co zapewni stabilne i efektywne spawanie.
- Upewnij się, że uchwyt spawalniczy jest mocno i bezpiecznie podłączony do systemu spawania.
- Sprawdź, czy miejsce podłączenia masy jest czyste i zapewnia dobrą przewodność.
- Dostosuj ustawienia prądu spawania, aby zapewnić stabilny przepływ energii elektrycznej.
Parametr | Wartość |
---|---|
Moc przyłącza maksymalna | 900 VA |
Prąd silnika (ciągły) | 6 A |
Prąd silnika (maksymalny) | 10 A |
Prędkość spawania | 0,1 – 2,0 m/min |
Prędkość jazdy (ręczna) | 2,0 m/min |
Prędkość podawania drutu | 0,3 – 25 m/min |
Wilgotność powietrza (maks.) | 95% |
Waga jednostki sterującej | 6,8 kg |
Waga kasety sterowniczej | 1,25 kg |
Przestrzeganie tych zasad pomoże Ci uzyskać stabilny przepływ prądu i zapewnić efektywne oraz wydajne spawanie, minimalizując przy tym powstawanie odprysków.
„Prawidłowe połączenie uchwytu spawalniczego i masy jest kluczowe dla zapewnienia stabilnego przepływu prądu i wydajności spawania.”
Zapewnienie stałego podawania drutu
Stabilne podawanie drutu spawalniczego ma kluczowe znaczenie dla uzyskania wysokiej jakości spoin. Odpowiednie wyposażenie uchwytu spawalniczego, właściwe rozłożenie przewodów oraz właściwy docisk rolek podajnika drutu to czynniki, które wpływają na stabilność tego procesu.
Odpowiednie wyposażenie uchwytu spawalniczego
Uchwyt spawalniczy powinien być wyposażony w odpowiedni prowadnik drutu oraz właściwie dobrany wlot drutu. Zapewnia to płynne i równomierne podawanie drutu do jeziorka spawalniczego, co przekłada się na stabilny łuk i minimalizację odprysków.
Właściwe rozłożenie pakietu przewodów
Pakiet przewodów zasilających uchwyt spawalniczy musi być ułożony w sposób zapobiegający ich splątaniu i załamywaniu. Rozłożenie przewodów ma duży wpływ na stabilne podawanie drutu i powinno być wykonane z dbałością o ten aspekt.
Odpowiedni docisk rolek podajnika drutu
Prawidłowy docisk rolek podajnika jest kluczowy dla stabilnego podawania drutu. Zbyt mały docisk może powodować poślizg drutu, a nadmierny docisk może deformować drut, utrudniając jego płynne podawanie. Właściwe ustawienie docisku to ważny element konfiguracji urządzenia spawalniczego.
„Stabilne podawanie drutu jest podstawą uzyskania wysokiej jakości spoin i minimalizacji odprysków podczas spawania.”
Prawidłowy dobór gazu osłonowego
Aby zapewnić efektywne i stabilne spawanie, kluczowe znaczenie ma właściwy dobór gazu osłonowego. Niewystarczająca ilość gazu może prowadzić do zakłóceń w stabilności łuku spawalniczego, co zwiększa ryzyko powstawania niepożądanych odprysków. Pamiętaj, że natężenie przepływu gazu w litrach na minutę powinno być równe średnicy drutu razy 10, aby zapewnić optymalną osłonę.
Właściwa ilość gazu
Przepływ gazu musi być dobrany odpowiednio do średnicy wykorzystywanego drutu spawalniczego. Zbyt mała ilość gazu sprawi, że spoina będzie narażona na zanieczyszczenia, co obniży jej jakość. Z kolei zbyt duży przepływ gazu może powodować turbulencje, które również negatywnie wpłyną na efekt spawania.
Krótki wolny wylot drutu dla efektywnej osłony gazowej
Równie ważne jest, aby długość wolnego wylotu drutu ze uchwytu spawalniczego była możliwie krótka. Zbyt długi wolny wylot drutu może sprawić, że osłona gazowa nie będzie skuteczna, co spowoduje powstawanie odprysków. Dlatego dba o to, aby ten element był właściwie dopasowany do Twoich potrzeb spawalniczych.
FAQ
Jak zmniejszyć zużycie energii w spawaniu?
Istnieje wiele możliwości oszczędzania energii w spawaniu, począwszy od energooszczędnej produkcji urządzeń spawalniczych, przez stosowanie trwałych, naprawialnych i nadających się do recyklingu urządzeń, aż po zoptymalizowane zużycie części eksploatacyjnych. Kluczową rolę w oszczędności energii odgrywają jednak nowoczesne, energooszczędne urządzenia spawalnicze i procesy spawania.
Czym charakteryzują się nowoczesne urządzenia inwertorowe?
Urządzenia inwertorowe zużywają nawet o jedną trzecią mniej energii niż stare, analogowe spawarki. Wynika to z faktu, że energia pobierana przez urządzenia inwertorowe jest faktycznie wykorzystywana do spawania, podczas gdy w przypadku urządzeń analogowych niemała ilość energii jest marnowana w postaci ciepła. Dodatkowo, dzięki mniejszym transformatorom urządzenia inwertorowe są bardziej kompaktowe, lżejsze i bardziej mobilne niż urządzenia analogowe.
Czy wszystkie urządzenia inwertorowe są tak samo energooszczędne?
Nawet wśród urządzeń inwertorowych występują mierzalne różnice pod względem zużycia energii. Funkcja korekcji współczynnika mocy w nowoczesnych urządzeniach inwertorowych pomaga zwiększyć współczynnik sprawności, co oznacza, że prawie cała pobierana energia jest wykorzystywana do spawania. Ponadto, najnowocześniejsze urządzenia inwertorowe zużywają mniej energii niż nieco starsze modele.
Jak cyfryzacja wpływa na efektywność energetyczną spawania?
Cyfrowe innowacje stanowią podstawę dla nowych, bardziej wydajnych metod i procesów spawania, które przekładają się na zmniejszenie zużycia energii. Przykładami są procesy CMT (Cold Metal Transfer) i PMC (Pulse Multi Control), które dzięki precyzyjnej regulacji i stabilnemu łukowi spawalniczemu minimalizują wypaczenie materiału podstawowego i zmniejszają ilość odrzutów, co wpływa na oszczędność energii.
Jak nowoczesne procesy spawania wpływają na zużycie energii?
Procesy spawania, które zapewniają większe prędkości spawania przy zachowaniu wysokiej stabilności łuku spawalniczego, również pozytywnie wpływają na zużycie energii. Przykładem jest proces PMC, który dzięki zoptymalizowanemu łukowi pulsującemu zapewnia o 15-20% większą prędkość spawania przy niezmienionym lub nawet wyższym poziomie jakości spoiny, co przekłada się na mniejsze wprowadzanie energii do materiału podstawowego.
Jak chłodzenie wpływa na zużycie energii w spawaniu?
Uchwyt spawalniczy większości wysokowydajnych urządzeń MIG/MAG jest chłodzony płynem, co nie zawsze jest energooszczędne. W wielu starszych urządzeniach płyn chłodzący krąży z tą samą prędkością, niezależnie od tego, ile energii jest doprowadzana do łuku spawalniczego. Chłodzenie dostosowane do wydajności oznacza, że chłodzenie jest powiązane ze zużyciem energii – używana jest tylko taka ilość energii, jaka jest potrzebna do uzyskania optymalnego rezultatu spawania, co pozwala uniknąć niepotrzebnego chłodzenia.
Co mogą zrobić sami spawacze, aby oszczędzać energię?
Spawacze mogą w znacznym stopniu przyczynić się do oszczędzania energii, decydując się na nowoczesne i energooszczędne urządzenie inwertorowe. Ponadto, zalecane jest skonfigurowanie w urządzeniu nowoczesnych procesów spawania, takich jak CMT czy PMC, dzięki którym spawanie może być prostsze, lepsze pod względem jakości i bardziej energooszczędne.
Jak zapewnić stały przepływ prądu podczas spawania?
Podstawowym warunkiem uniknięcia odprysków przy spawaniu jest zapewnienie stałego przepływu prądu. W tym celu uchwyt spawalniczy wraz z przewodem masy musi być mocno połączony z systemem spawania, a miejsce zamocowania i zacisk masy muszą być odsłonięte i odznaczać się dobrą przewodnością, aby mógł płynąć prąd.
Jak zapewnić stabilne podawanie drutu?
Stabilność łuku spawalniczego, a co za tym idzie – minimalizacja odprysków, zależy również od stałego podawania drutu. Wymaga to odpowiedniego wyposażenia uchwytu spawalniczego (prowadnik drutu, wlot), prostego rozłożenia pakietu przewodów oraz właściwego docisku rolek podajnika drutu.
Jak dobrać prawidłową ilość gazu osłonowego?
Niewystarczająca ilość gazu osłonowego może zakłócać stabilność łuku spawalniczego, co prowadzi do powstawania odprysków. Obowiązuje zasada, że natężenie przepływu gazu w litrach na minutę powinno być równe średnicy drutu razy 10. Ponadto, wolny wylot drutu nie może być zbyt długi, aby osłona gazowa była skuteczna.