Temperatura strumienia plazmy używanego w procesie cięcia plazmowego może sięgać nawet 30 000 stopni Celsjusza. To właśnie ta niezwykła właściwość plazmy umożliwia efektywne cięcie szerokiej gamy materiałów, w tym bardzo twardych i grubych. Cięcie plazmowe to technologia, która została opracowana już w latach 50. ubiegłego wieku, a od tego czasu znacznie się rozwinęła, znajdując zastosowanie w wielu gałęziach przemysłu.
Niezależnie od tego, czy wykorzystujesz cięcie plazmowe do produkcji precyzyjnych komponentów w przemyśle lotniczym, czy w ramach swojego hobby, istnieje wiele sposobów, aby zoptymalizować ten proces i uzyskać jeszcze lepsze rezultaty. W niniejszym artykule przyjrzymy się bliżej tajnikom efektywnego cięcia plazmowego i poznamy sposoby na poprawę wydajności tego procesu.
Kluczowe informacje:
- Cięcie plazmowe umożliwia precyzyjne cięcie metali o różnej grubości
- Technologia ta jest stosowana w wielu branżach, w tym w przemyśle lotniczym i kosmicznym
- Regularna konserwacja i wymiana dysz przecinarki plazmowej to kluczowe czynniki wpływające na jakość cięcia
- Właściwy dobór parametrów procesu, takich jak natężenie prądu, napięcie łuku czy prędkość cięcia, umożliwia optymalizację procesu
- Nowoczesne maszyny cięcia plazmowego charakteryzują się wyższą efektywnością energetyczną i lepszą filtracją powietrza
Co to jest cięcie plazmą?
Cięcie plazmą to technologia wykorzystująca silnie skoncentrowany łuk elektryczny jako źródło ciepła do topienia i wydmuchiwania materiału ze szczeliny cięcia. Proces ten umożliwia obróbkę wszystkich materiałów dobrze przewodzących prąd elektryczny, takich jak stal, żeliwo, aluminium czy miedź.
Historia i rozwój technologii cięcia plazmowego
Technologia cięcia plazmowego nieustannie się rozwija, pozwalając na ciecie materiałów o coraz większych grubościach przy zachowaniu wysokiej jakości. Historia cięcia plazmowego sięga lat 50. XX wieku, kiedy to zaczęło ono zastępować tradycyjne metody cięcia gazowego. Od tego czasu technologia ta zdobyła szerokie zastosowanie w wielu gałęziach przemysłu, między innymi dzięki ciągłemu ulepszaniu parametrów procesu.
Zalety cięcia plazmowego w różnych branżach przemysłowych
Cięcie plazmą charakteryzuje się wysoką prędkością procesu, zwłaszcza w przypadku obróbki blach o mniejszych grubościach. Dodatkowo, nie ma potrzeby wstępnego podgrzewania materiału, co przekłada się na oszczędność czasu. Ponadto, cięcie plazmą jest bardziej efektywne kosztowo w porównaniu do tradycyjnego cięcia gazowego. Technologia ta znalazła zastosowanie m.in. w branży metalowej, budowlanej, stoczniowej oraz w przemyśle ciężkim, zapewniając dobrą jakość cięcia przy stosunkowo niskich kosztach eksploatacyjnych.
„Około 85% użytkowników wycinarek plazmowych preferuje korzystanie z powietrza jako gazu do cięcia, głównie ze względu na jego dostępność i niską cenę.”
Zasada działania cięcia plazmowego
Cięcie plazmowe to zaawansowana technologia, której podstawą jest wykorzystanie właściwości plazmy – zjonizowanej materii o stanie skupienia przypominającym gaz. Plazma składa się zarówno z naładowanych elektrycznie cząstek, jak i cząstek obojętnych. Obecność dużej ilości jonów o różnym ładunku oraz swobodnych elektronów sprawia, że plazma przewodzi prąd elektryczny i przy odpowiednio wysokim natężeniu emituje energię w postaci światła i ciepła.
Właściwości plazmy jako stanu materii
Właśnie ta charakterystyczna cecha plazmy jest wykorzystywana w procesie cięcia plazmowego. Silnie skoncentrowany łuk elektryczny jarzący się pomiędzy ciętym materiałem a elektrodą stanowi źródło ciepła, które pozwala na stopienie i wydmuchanie materiału ze szczeliny cięcia. Dzięki temu cięcie plazmowe może być wykonywane na różnych, przewodzących prąd elektryczny materiałach, takich jak stal, aluminium czy miedź.
Źródło ciepła w procesie cięcia plazmowego
Podczas pracy przecinarki plazmowej zasilanie pochodzi z sieci elektrycznej i generuje prąd stały o napięciu 240–400 V. Obwód generatora wysokich częstotliwości wytwarza napięcie zmienne od 5 do 10 kV o częstotliwości 2 MHz. Dla palników plazmy powietrznej wystarczy zbliżyć dyszę do materiału, aby rozpocząć cięcie, które odbywa się przy bardzo wysokich temperaturach od 10 tys. do 30 tys. K.
Właściwości | Wartości |
---|---|
Napięcie zasilania | 240-400 V (prąd stały) |
Napięcie generatora wysokich częstotliwości | 5-10 kV (prąd zmienny, 2 MHz) |
Temperatura cięcia | 10 000 – 30 000 K |
Dzięki tym parametrom, technologia cięcia plazmowego umożliwia obróbkę różnych materiałów przewodzących prąd elektryczny, takich jak stal węglowa, żeliwo, stal kwasoodporna, aluminium, stopy aluminium oraz mosiądz.
Elementy systemu plazmowego
System cięcia plazmowego składa się z kilku kluczowych elementów, które zapewniają jego prawidłowe i efektywne działanie. Elementy systemu cięcia plazmowego obejmują:
- Źródło zasilania (tzw. źródło plazmowe) – zapewnia energię elektryczną niezbędną do generowania łuku plazmowego.
- Palnik plazmowy – odpowiada za wytworzenie i kontrolę strumienia plazmy tnącej.
- Przewód uziemiający – łączy obrabiane materiały z ujemnym biegunem źródła zasilania.
- Części eksploatacyjne, takie jak dysze, elektrody czy osłony – wymagające regularnej wymiany w celu zapewnienia optymalnej wydajności cięcia.
W przypadku systemów plazmowych wąskostrumieniowych, dodatkowo stosowane są konsole gazowe do precyzyjnego dozowania i mieszania gazów technicznych, które mają kluczowe znaczenie dla jakości cięcia.
Element systemu | Opis | Znaczenie |
---|---|---|
Źródło zasilania | Zapewnia energię elektryczną do generowania łuku plazmowego | Podstawowy element umożliwiający powstanie i utrzymanie procesu cięcia plazmowego |
Palnik plazmowy | Wytwarza i kontroluje strumień plazmy tnącej | Bezpośrednio realizuje cięcie materiału poprzez wysokotemperaturowy strumień plazmy |
Przewód uziemiający | Łączy obrabiane materiały z ujemnym biegunem źródła zasilania | Zamyka obwód elektryczny umożliwiając przepływ prądu niezbędnego do cięcia |
Części eksploatacyjne | Elementy takie jak dysze, elektrody czy osłony, wymagające regularnej wymiany | Zapewniają optymalną wydajność i jakość cięcia przez cały okres eksploatacji |
Konsole gazowe | Dozują i mieszają gazy techniczne w systemach plazmowych wąskostrumieniowych | Umożliwiają precyzyjną kontrolę parametrów gazu tnącego, kluczową dla jakości cięcia |
Prawidłowe działanie systemu cięcia plazmowego wymaga zatem zapewnienia zarówno zasilania elektrycznego, jak i odpowiedniego doprowadzenia gazów technicznych do palnika. Zintegrowanie tych kluczowych elementów systemu cięcia plazmowego jest fundamentalne dla uzyskania wysokiej jakości i wydajności procesów cięcia.
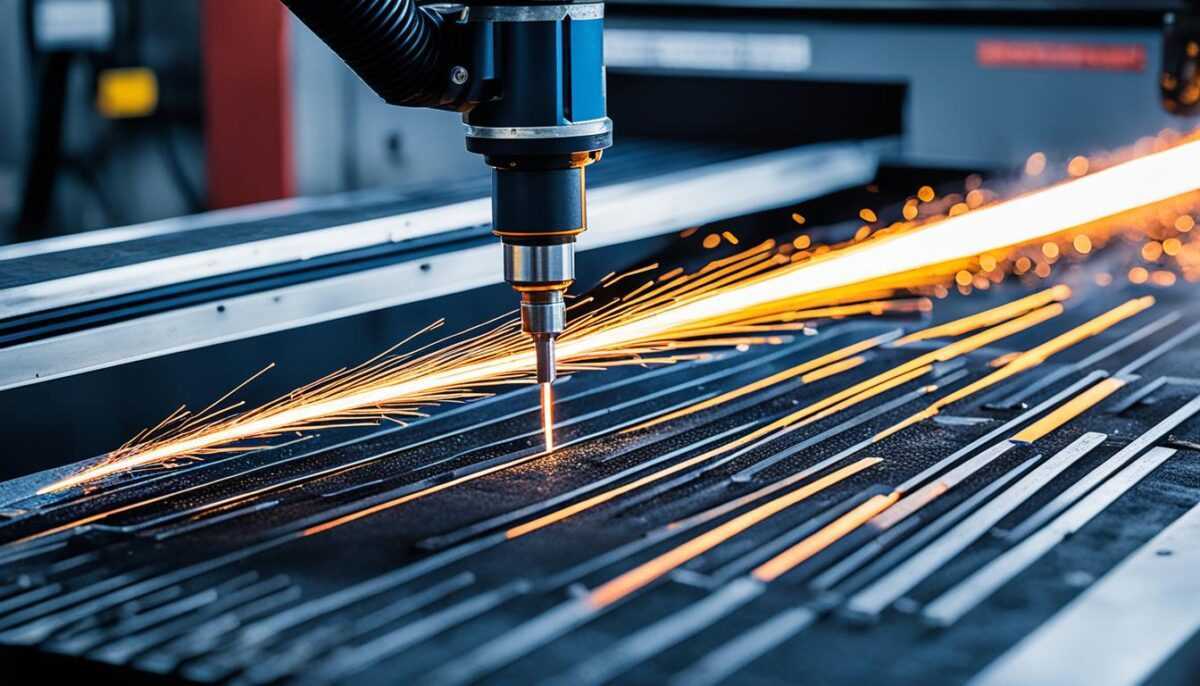
Parametry wpływające na proces cięcia plazmowego
Precyzyjne cięcie plazmowe wymaga starannego doboru kluczowych parametrów, takich jak natężenie prądu cięcia, napięcie łuku plazmowego, prędkość cięcia oraz grubość ciętego materiału. Każdy z nich odgrywa kluczową rolę w uzyskaniu wysokiej jakości efektu końcowego.
Natężenie prądu cięcia
Natężenie prądu cięcia decyduje o temperaturze i energii łuku plazmowego, bezpośrednio wpływając na możliwą do osiągnięcia grubość cięcia oraz prędkość procesu. Wyższa wartość prądu pozwala na cięcie grubszych materiałów z większą wydajnością.
Napięcie łuku plazmowego
Napięcie łuku plazmowego, wahające się zazwyczaj od 50 do 200 V, ma kluczowe znaczenie dla sprawnego przebiegu cięcia. Odpowiednie napięcie zapewnia efektywną jonizację i właściwe procesy zachodzące podczas cięcia.
Prędkość cięcia
Prędkość cięcia musi być dobrana proporcjonalnie do natężenia prądu i grubości materiału, aby osiągnąć optymalną jakość. Zbyt niska prędkość może prowadzić do powstawania nierównych krawędzi, natomiast zbyt wysoka może skutkować niedokładnym przebiciem materiału.
Grubość ciętego materiału
Grubość ciętego materiału jest kluczowym parametrem, determinującym dobór pozostałych elementów procesu. Właściwe dostosowanie natężenia prądu, napięcia i prędkości cięcia do grubości obrabianego elementu zapewnia uzyskanie pożądanej jakości.
Odpowiednie wyważenie tych parametrów jest kluczowe dla zagwarantowania optymalnych efektów cięcia plazmowego, pozwalając na uzyskanie precyzyjnych i wysokiej jakości elementów konstrukcyjnych w wielu gałęziach przemysłu.
Optymalizacja procesu cięcia plazmowego
Aby zoptymalizować proces cięcia plazmowego, należy skupić się na doborze odpowiednich parametrów technologicznych. Kluczową rolę odgrywają takie czynniki, jak natężenie prądu cięcia, prędkość cięcia oraz odległość palnika od ciętego materiału. Prawidłowe ustawienie tych parametrów pozwala na uzyskanie wysokiej jakości krawędzi cięcia, przy jednoczesnym zachowaniu wydajności procesu.
Dobór odpowiednich parametrów procesu
Istotne jest, aby zoptymalizować następujące parametry cięcia plazmowego:
- Natężenie prądu cięcia – odpowiada za głębokość wnikania plazmy w materiał i wpływa na jakość krawędzi
- Prędkość cięcia – decyduje o wydajności procesu i wpływa na jakość krawędzi ciętego elementu
- Odległość palnika od ciętego materiału – ma wpływ na stabilność łuku plazmowego i precyzję cięcia
Technologie SureCut firmy Hypertherm
Firma Hypertherm, będąca liderem w branży systemów plazmowych, opracowała szereg zaawansowanych technologii usprawniających optymalizację procesu cięcia plazmowego. Rozwiązania te, takie jak True Hole, True Bevel, Rapid Part czy Plate Saver, automatycznie dostrajają kluczowe parametry cięcia, poprawiając jakość, wydajność i powtarzalność procesu.
Technologie SureCut firmy Hypertherm wykorzystują możliwości wysokiej klasy systemów plazmowych XPR i HPR, oferując gotowe, fabrycznie przetestowane konfiguracje, które pozwalają zoptymalizować cięcie bez konieczności przeprowadzania żmudnych prób i eksperymentów. Pozwala to na znaczne zmniejszenie zaangażowania operatora i gwarantuje lepsze efekty cięcia.
Zalety zoptymalizowanego procesu cięcia plazmowego
Optymalizacja procesu cięcia plazmowego przy użyciu zaawansowanych technologii, takich jak te opracowane przez firmę Hypertherm, przynosi szereg korzyści. Pozwala ona na uzyskanie znacznie lepszej jakości cięcia, w tym wyższej powtarzalności i dokładności kształtów, a także eliminuje konieczność dodatkowej obróbki gotowych elementów.
Jednocześnie zoptymalizowany proces charakteryzuje się wyższą wydajnością, skracając czas cyklu cięcia i zwiększając liczbę produkowanych części. Przekłada się to również na oszczędności materiałowe oraz niższe koszty eksploatacji. W efekcie optymalizacja prowadzi do wzrostu konkurencyjności firmy i zwiększenia jej zysków.
Korzyści z zoptymalizowanego cięcia plazmowego |
---|
|
Zoptymalizowane zalety cięcia plazmowego poprzez zastosowanie zaawansowanych technologii, takich jak te oferowane przez Hypertherm, pozwalają firmom na zwiększenie wydajności, jakości i rentowności procesów produkcyjnych.
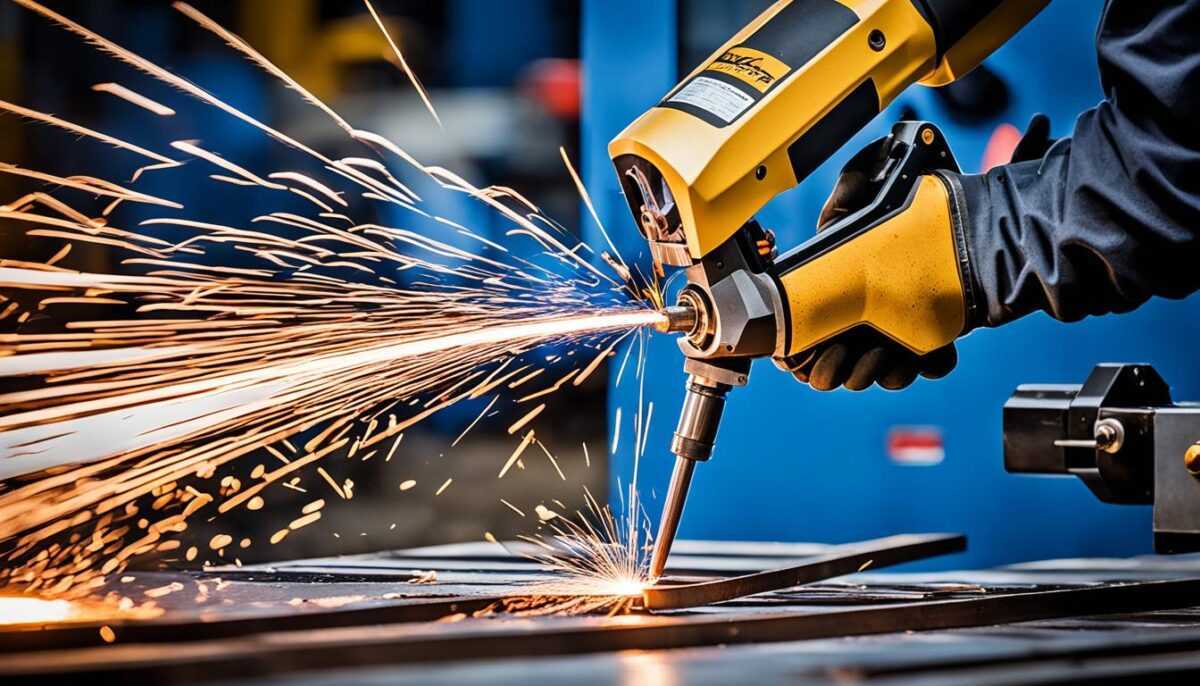
Optymalizacja procesu cięcia plazmowego
Kluczem do uzyskania wysokiej efektywności i wydajności w procesie optymalizacja cięcia plazmowego jest właściwe dostosowanie jego parametrów. Istotne są takie czynniki, jak natężenie prądu, prędkość cięcia oraz odległość palnika od ciętego materiału. Odpowiednie ustawienie tych elementów zapewnia najwyższą poprawa efektywności cięcia plazmowego.
Pomocne w tym mogą być zaawansowane technologie, takie jak te oferowane przez firmę Hypertherm. Ich rozwiązania automatycznie dostrajają parametry cięcia, optymalizując ten proces i poprawiając jego efektywność. Dzięki temu można uzyskać wysoką jakość cięcia, zwiększyć wydajność i jednocześnie obniżyć koszty.
Istotne jest również stosowanie wysokiej jakości materiałów eksploatacyjnych, takich jak dysze i elektrody. Prawidłowe ustawienie i prowadzenie palnika pozwala na uzyskanie optymalnych rezultatów. Odpowiednia optymalizacja procesu cięcia plazmowego przekłada się na wymierne korzyści – wyższą jakość wykonania, większą wydajność i redukcję kosztów.
„Właściwy dobór parametrów cięcia plazmowego to klucz do sukcesu. Automatyczne systemy regulacji pomagają osiągnąć najwyższą efektywność procesu.”
Porady dla operatorów maszyn do cięcia plazmowego
Aby zapewnić wysoką jakość i wydajność procesu cięcia plazmowego, operatorzy maszyn powinni zwracać szczególną uwagę na kilka kluczowych kwestii. Jednym z najważniejszych aspektów jest upewnienie się, że łuk plazmowy wykonuje cięcie w odpowiednim kierunku i że wybrany proces jest odpowiedni do rodzaju oraz grubości ciętego materiału.
Regularnie kontroluj stan zużycia materiałów eksploatacyjnych, takich jak dysze i elektrody, oraz utrzymuj prawidłowe ustawienie i prowadzenie palnika względem ciętego elementu. Prawidłowe dobranie parametrów, jak prędkość cięcia, pozwoli uniknąć typowych problemów, takich jak powstawanie nadmiernej ilości żużlu lub niecałkowite przebicie materiału.
Najczęstsze nieprawidłowości i sposoby ich zapobiegania
- Nieprawidłowe ustawienie palnika – Upewnij się, że palnik jest ustawiony w odpowiedniej odległości i kącie względem ciętego materiału.
- Zużycie materiałów eksploatacyjnych – Regularnie kontroluj i wymieniaj zużyte dysze, elektrody oraz inne części.
- Błędny dobór parametrów cięcia – Dostosuj prędkość cięcia, natężenie prądu i inne ustawienia do danego materiału i grubości.
- Nieprawidłowe prowadzenie palnika – Utrzymuj stałą, stabilną prędkość oraz odpowiedni kąt palnika podczas cięcia.
- Niewystarczająca wentylacja – Zapewnij dobrą wentylację, aby minimalizować narażenie na szkodliwe opary.
Przestrzegając tych zaleceń, operatorzy maszyn do cięcia plazmowego mogą znacznie ograniczyć występowanie problemów oraz zapewnić wysoką jakość i wydajność wykonywanej pracy.
Wniosek
Cięcie plazmowe to zaawansowana technologia, która znalazła szerokie zastosowanie w przemyśle dzięki ciągłemu rozwojowi i udoskonalaniu. Aby w pełni wykorzystać potencjał tej metody, kluczowe jest właściwe zoptymalizowanie procesu cięcia poprzez dobór optymalnych parametrów, takich jak natężenie prądu, prędkość cięcia czy odległość palnika. Pomocne w tym mogą być zaawansowane technologie, takie jak te opracowane przez firmę Hypertherm, które automatycznie dostrajają parametry, poprawiając jakość, wydajność i powtarzalność cięcia.
Dzięki podsumowaniu optymalizacji cięcia plazmowego, firmy mogą uzyskać wymierne korzyści, takie jak zwiększenie produktywności, obniżenie kosztów oraz wzmocnienie swojej konkurencyjności na rynku. Optymalizacja procesu cięcia plazmowego jest kluczowa dla osiągnięcia optymalnych wyników i zapewnienia wysokiej efektywności produkcyjnej.
Podsumowując, podsumowanie optymalizacji cięcia plazmowego to niezbędny element w dążeniu do maksymalizacji efektywności i konkurencyjności przedsiębiorstw wykorzystujących tę zaawansowaną technologię.
FAQ
Jak zwiększyć jakość i wydajność cięcia plazmowego?
Kluczem jest optymalizacja procesu poprzez właściwy dobór parametrów, takich jak natężenie prądu, prędkość cięcia czy odległość palnika od materiału. Pomocne mogą być zaawansowane technologie, które automatycznie dostrajają te parametry, poprawiając jakość, wydajność i powtarzalność cięcia.
Jakie są główne elementy systemu cięcia plazmowego?
W skład systemu cięcia plazmowego wchodzą m.in. źródło zasilania, palnik plazmowy, przewód uziemiający oraz części eksploatacyjne, takie jak dysze, elektrody i osłony.
Jakie są kluczowe parametry wpływające na proces cięcia plazmowego?
Najważniejsze parametry to natężenie prądu cięcia, napięcie łuku plazmowego, prędkość cięcia oraz grubość ciętego materiału. Odpowiednie dobranie tych parametrów ma kluczowe znaczenie dla uzyskania dobrej jakości cięcia.
Jakie korzyści daje optymalizacja procesu cięcia plazmowego?
Optymalizacja pozwala uzyskać znacznie lepszą jakość cięcia, w tym wyższą powtarzalność i dokładność kształtów, zwiększyć wydajność procesu, skracając czas cyklu cięcia, a także osiągnąć oszczędności materiałowe i niższe koszty eksploatacji.
Na co powinni zwracać uwagę operatorzy maszyn do cięcia plazmowego?
Kluczowe jest sprawdzanie, czy łuk plazmowy wykonuje cięcie w odpowiednim kierunku, regularne kontrolowanie zużycia materiałów eksploatacyjnych oraz prawidłowe ustawienie i prowadzenie palnika. Ważne jest również dobranie odpowiedniej prędkości cięcia, aby uniknąć problemów, takich jak nadmierne tworzenie się żużlu lub niecałkowite przebicie materiału.