Współczesne maszyny CNC wymagają stałej kontroli i konserwacji, a olej chłodzący odgrywa kluczową rolę w ich prawidłowym działaniu. Zgodnie z badaniami, aż 95% awarii maszyn CNC jest spowodowanych problemami z systemem chłodzenia. Odpowiednie chłodzenie nie tylko wydłuża żywotność narzędzi i samej maszyny, ale także zapobiega przegrzewaniu się, które może prowadzić do kosztownych napraw. Dlatego wybór właściwego systemu chłodzenia CNC ma kluczowe znaczenie dla efektywności i wydajności Twojej produkcji.
Kluczowe wnioski:
- Nowoczesne maszyny CNC wymagają stałej kontroli i konserwacji, a olej chłodzący jest kluczowy dla ich prawidłowego funkcjonowania.
- Odpowiednie chłodzenie wydłuża żywotność narzędzi i samej maszyny, a także zapobiega przegrzewaniu się, które może prowadzić do kosztownych napraw.
- Wybór właściwego systemu chłodzenia CNC ma kluczowe znaczenie dla efektywności i wydajności Twojej produkcji.
- Systemy chłodzenia CNC działają poprzez cyrkulację oleju przez specjalne wymienniki ciepła, które rozpraszają nadmiar ciepła na zewnątrz maszyny.
- Inwestycja w nowoczesne systemy chłodzenia oleju do maszyn CNC zwiększa efektywność, oszczędność energii oraz umożliwia monitorowanie i regulację temperatury w czasie rzeczywistym.
Wprowadzenie do systemów chłodzenia CNC
Układy chłodzenia odgrywają kluczową rolę w prawidłowym funkcjonowaniu maszyn CNC. Utrzymują one optymalną temperaturę silnika, wpływając pozytywnie na spalanie i emisję zanieczyszczeń. Można wyróżnić dwa podstawowe rodzaje systemów chłodzenia: chłodzenie bezpośrednie (z wykorzystaniem powietrza) oraz chłodzenie pośrednie (z użyciem cieczy chłodzącej).
Znaczenie chłodzenia maszyn CNC
Podczas procesu skrawania ponad 95% energii przetwarzane jest na ciepło, pochłaniając wióry. Aż 80% tego ciepła ulega przetworzeniu, dlatego tak istotne jest efektywne chłodzenie maszyny. Chłodziwa do obrabiarek mają za zadanie m.in. schładzanie narzędzia i powierzchni ciętego materiału oraz zmniejszanie tarcia.
Rodzaje systemów chłodzenia
Można wyróżnić dwa główne rodzaje systemów chłodzenia maszyn CNC:
- Chłodzenie bezpośrednie – wykorzystuje powietrze do odprowadzania ciepła.
- Chłodzenie pośrednie – używa cieczy chłodzącej, która następnie odprowadza ciepło.
Wybór odpowiedniego systemu chłodzenia zależy od wielu czynników, takich jak rodzaj obrabianego materiału, intensywność obróbki czy wymagania co do dokładności i wykończenia powierzchni.
Układy chłodzenia bezpośredniego
Układy chłodzenia bezpośredniego w maszynach CNC wykorzystują powietrze do efektywnego schładzania silników i komponentów. Kluczowym elementem tej metody jest odpowiednie ukształtowanie żebrowania głowicy i cylindra, co pozwala na szybkie i skuteczne nagrzewanie się silnika podczas obróbki.
Główną zaletą układów chłodzenia bezpośredniego jest ich prostota konstrukcji i niska awaryjność. Powietrze, jako medium chłodzące, jest łatwo dostępne i nie wymaga skomplikowanych systemów dystrybucji, jak w przypadku chłodzenia pośredniego.
Parametr | Układy chłodzenia bezpośredniego | Układy chłodzenia pośredniego |
---|---|---|
Środek chłodzący | Powietrze | Ciecze chłodzące (woda, olej) |
Złożoność konstrukcji | Prosta | Złożona |
Koszt eksploatacji | Niski | Wyższy |
Efektywność chłodzenia | Umiarkowana | Wysoka |
Chłodzenie powietrzem jest szczególnie przydatne w maszynach CNC o niewielkich gabarytach i mocach, gdzie nie jest wymagana najwyższa wydajność termiczna. Układ taki charakteryzuje się także niższymi kosztami inwestycyjnymi i eksploatacyjnymi.
Nowoczesne konstrukcje maszyn CNC coraz częściej wykorzystują połączone układy chłodzenia bezpośredniego i pośredniego, zapewniając optymalną wydajność i niezawodność przy zachowaniu atrakcyjnych kosztów.
Układy chłodzenia pośredniego
Układy chłodzenia pośredniego to rozwiązanie, które wykorzystuje ciecz chłodzącą do regulowania temperatury podczas obróbki CNC. W przeciwieństwie do bezpośredniego chłodzenia, w którym czynnik chłodzący jest w bezpośrednim kontakcie z obrabianym elementem, w przypadku chłodzenia pośredniego ciecz krąży w zamkniętym układzie, odizolowana od miejsca skrawania.
Komponenty układu chłodzenia pośredniego
Podstawowymi elementami układu chłodzenia pośredniego są:
- Zbiornik na chłodziwo
- Pompa chłodziwa
- Przewody
- Dysze
Ciecz chłodząca jest stale recyrkulowana, przepływając przez wymiennik ciepła, gdzie następuje jej ochłodzenie, a następnie dostarczana do miejsca obróbki.
Zalety chłodzenia pośredniego
Główną zaletą układów chłodzenia pośredniego jest stabilna temperatura podczas obróbki CNC. Dzięki temu znacznie zwiększa się żywotność maszyny i narzędzi, a także poprawia się jakość obrabianej powierzchni. Dodatkowo, chłodzenie pośrednie zapewnia lepszą kontrolę nad temperaturą, co przekłada się na większą wydajność i powtarzalność procesu.
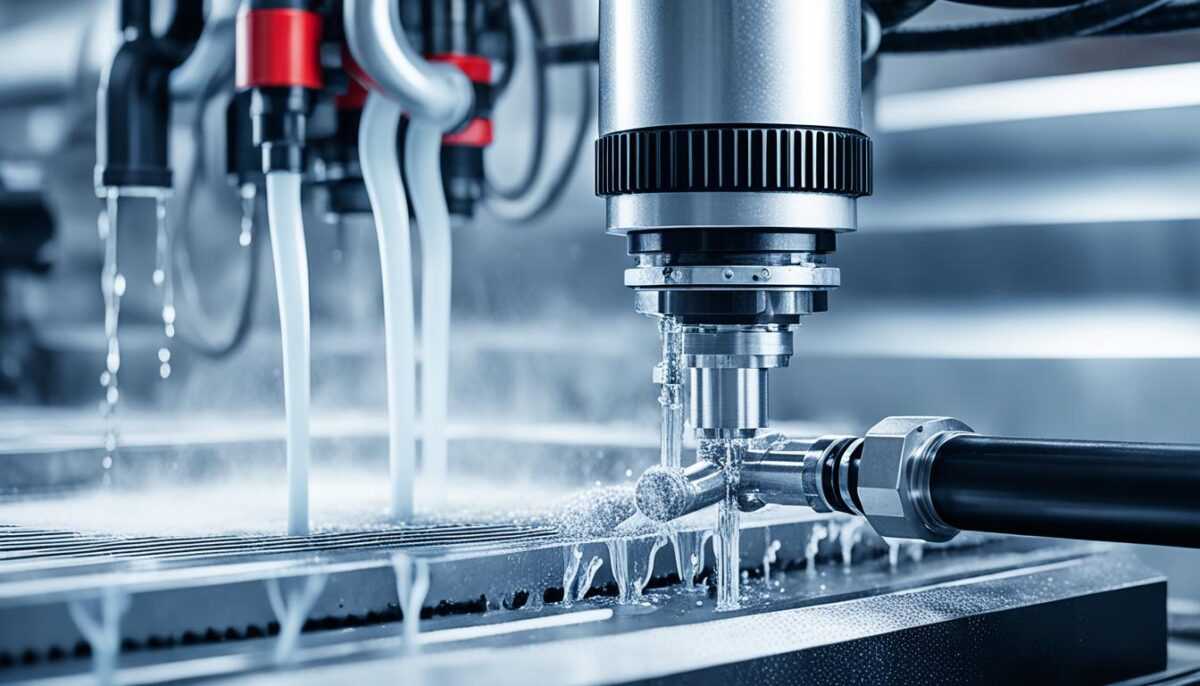
„Oszczędności energii elektrycznej w systemach chłodzenia adiabatycznego sięgają 80–90% w porównaniu do systemów sprężarkowych.”
Podsumowując, układy chłodzenia pośredniego to skuteczne rozwiązanie, zapewniające stabilne warunki termiczne podczas obróbki CNC, co przekłada się na wydłużenie żywotności maszyny i narzędzi oraz poprawę jakości wykonywanej pracy.
Wydajność i wymagania chłodzenia CNC
Skuteczne chłodzenie jest kluczowym elementem wydajnej obróbki CNC. Wydajność chłodzenia CNC musi być dokładnie dobrana do specyfiki danej maszyny oraz procesu obróbki. Czynniki takie jak moc obrabiarki, rodzaj obrabianego materiału czy czas pracy mają kluczowe znaczenie dla odpowiedniego dopasowania systemu chłodzenia.
Materiały o wysokiej odporności termicznej i niskiej przewodności cieplnej, takie jak tytan, wymagają specjalnie zaprojektowanych cieczy chłodzących, zawierających efektywne środki smarujące i chłodzące. Pozwala to na zwiększenie wydajności i zapobieganie przyleganiu narzędzia, wydłużając jego żywotność. Z kolei w przemyśle motoryzacyjnym, wysokociśnieniowe dodatki do cieczy obróbczych tworzą ochronną warstwę na powierzchni narzędzie-przedmiot, ograniczając zużycie i spawanie, poprawiając efektywność skrawania, szczególnie w przypadku wysokowytrzymałych stali nierdzewnych.
Wymagania chłodzenia CNC obejmują również zrównoważenie wydajności i jakości. Odpowiedni dobór prędkości skrawania (Vc), głębokości skrawania (ap) oraz posuwu (f) ma kluczowe znaczenie dla zoptymalizowania procesu obróbki CNC, minimalizując ryzyko uszkodzenia narzędzi. Nowoczesne narzędzia symulacyjne i projektowe, takie jak Mastercam, SolidWorks CAM czy Fusion 360, pozwalają na zaawansowane modelowanie i optymalizację parametrów skrawania.
Parametr | Wpływ na wydajność i wymagania chłodzenia |
---|---|
Prędkość skrawania (Vc) | Bezpośrednio wpływa na prędkość produkcji i trwałość narzędzia |
Głębokość skrawania (ap) | Wpływa na siłę skrawania i generowanie ciepła, wymagając efektywnego chłodzenia |
Posuw (f) | Wpływa na jakość powierzchni i prędkość skrawania, wymagając optymalnego dopasowania |
Stałe doskonalenie procesów obróbki CNC, przy jednoczesnej poprawie wydajności i jakości, to kluczowe wyzwanie, wymagające kompleksowego podejścia do optymalizacji chłodzenia, eliminacji przestojów, redukcji odpadów i zarządzania złożonością. Zaawansowane techniki, takie jak adaptacyjne programowanie i analiza danych przy użyciu uczenia maszynowego, stanowią ważne narzędzia do zoptymalizowania obróbki CNC.
Znaczenie chłodzenia oleju w maszynach CNC
Chłodzenie oleju odgrywa kluczową rolę w zapewnieniu długiej żywotności maszyn CNC. Prawidłowe utrzymanie stałej temperatury oleju smarującego gwarantuje właściwe smarowanie i chłodzenie kluczowych komponentów maszyny. Skutkuje to dłuższą żywotnością narzędzi skrawających oraz całej obrabiarki, a także zapobiega jej przegrzewaniu się.
Zalety chłodzenia oleju
- Wydłużenie żywotności narzędzi i całej maszyny CNC
- Zapobieganie przegrzewaniu się obrabiarki
- Utrzymanie optymalnej temperatury oleju smarującego
- Zapewnienie właściwego smarowania kluczowych komponentów
Działanie systemów chłodzenia oleju
Systemy chłodzenia oleju w maszynach CNC działają na zasadzie przepływu oleju przez wymienniki ciepła. Nadmiar ciepła generowany podczas obróbki jest odprowadzany na zewnątrz, co pozwala utrzymać optymalną temperaturę oleju. Dzięki temu zapewnione jest właściwe smarowanie i chłodzenie, co przekłada się na wydajność i żywotność całego systemu.
Korzyść | Opis |
---|---|
Wydłużona żywotność narzędzi | Prawidłowe chłodzenie oleju zapobiega przedwczesnemu zużywaniu się narzędzi skrawających, zwiększając ich trwałość nawet o 300%. |
Lepsza wydajność obróbki | Zastosowanie odpowiedniego systemu chłodzenia oleju może zwiększyć prędkość obróbki nawet o 30%. |
Ochrona maszyny | Utrzymywanie optymalnej temperatury oleju chroni kluczowe podzespoły maszyny CNC przed przegrzaniem i uszkodzeniem. |
Odpowiednio zaprojektowany i zintegrowany system chłodzenia oleju w maszynach CNC to gwarancja wydajnej, bezawaryjnej i długotrwałej pracy całego urządzenia. Inwestując w ten element, można znacznie poprawić wydajność i żywotność procesu obróbki CNC.
Wybór systemu chłodzenia CNC
Dokonanie właściwego wyboru systemu chłodzenia do maszyny CNC jest kluczowe dla zapewnienia jej efektywnej i niezawodnej pracy. Na rynku dostępnych jest wiele różnorodnych rozwiązań, różniących się między sobą wydajnością, pojemnością, a także ceną. Przed podjęciem decyzji warto dokładnie przeanalizować potrzeby własnego zakładu i skonsultować się z ekspertami, aby dobrać system chłodzenia optymalny dla danej maszyny oraz procesu produkcyjnego.
Czynniki wpływające na wybór
Przy wyborze systemu chłodzenia wybór systemu chłodzenia CNC należy wziąć pod uwagę kilka kluczowych czynników:
- Moc i wydajność maszyny CNC – system chłodzenia musi być dostosowany do mocy oraz obciążenia urządzenia, aby zapewnić skuteczne odprowadzanie ciepła.
- Czynniki wyboru systemu chłodzenia – takie jak temperatura otoczenia, wilgotność powietrza, czy też stopień zanieczyszczenia środowiska produkcyjnego.
- Wymagania dotyczące czystości chłodziwa – niektóre procesy obróbka CNC wymagają użycia ultra czystego chłodziwa.
- Dostępna powierzchnia na rozmieszczenie elementów systemu chłodzenia.
- Budżet przeznaczony na inwestycję – układy chłodzenia różnią się znacząco ceną.
Kompleksowa analiza tych czynników pozwoli na wybór systemu chłodzenia, który zapewni optymalną wydajność i niezawodność maszyny CNC przy jednoczesnej minimalizacji kosztów eksploatacji.
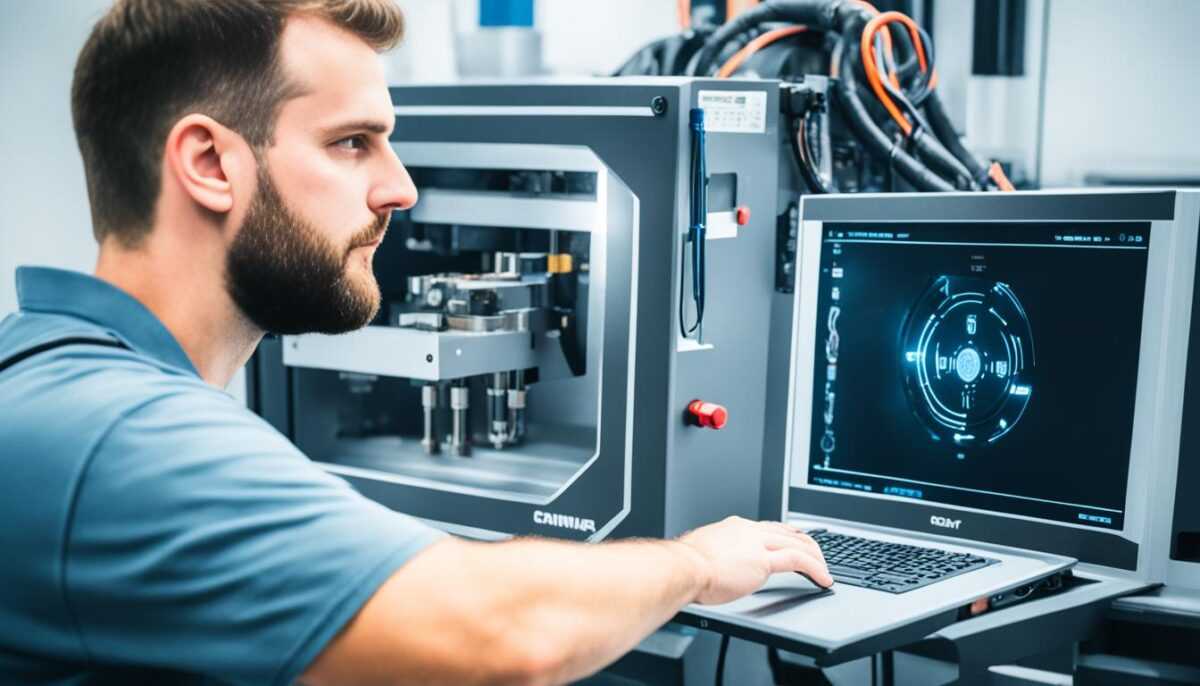
„Skuteczne chłodzenie maszyny CNC to klucz do jej długotrwałej i efektywnej pracy. Warto poświęcić czas na właściwy dobór systemu chłodzenia, by uzyskać maksymalne korzyści z inwestycji.”
Kompresory śrubowe wspomagające chłodzenie CNC
Kompresory śrubowe przemysłowe odgrywają kluczową rolę we wspieraniu procesów obróbki CNC. Dostarczają one niezawodne źródło sprężonego powietrza, które jest wykorzystywane do napędzania narzędzi pneumatycznych, systemów chłodzenia, usuwania wiórów i pyłu, a także do zaciskania i mocowania obrabianych przedmiotów. Odpowiedni dobór kompresora śrubowego ma istotne znaczenie dla wydajności i bezpieczeństwa maszyn CNC.
Zastosowania sprężonego powietrza w CNC
Sprężone powietrze dostarczane przez kompresory śrubowe ma szerokie zastosowania w obróbce CNC:
- Napędzanie narzędzi pneumatycznych, takich jak wiertarki, szlifierki i frezarki
- Chłodzenie narzędzi i obrabianych elementów, zapewniając efektywne odprowadzanie ciepła
- Usuwanie wiórów, pyłu i opiłków powstających podczas obróbki, utrzymując czystość środowiska pracy
- Zaciskanie i mocowanie obrabianych przedmiotów na stołach roboczych maszyn CNC
Kompresory śrubowe zapewniają stabilne i niezawodne źródło sprężonego powietrza, niezbędne do sprawnego funkcjonowania nowoczesnych systemów CNC.
Parametr | Zakres |
---|---|
Ciśnienie robocze | 7-13 bar |
Wydajność | 1,5-30 m³/min |
Moc silnika | 2,2-75 kW |
Poziom hałasu | 65-75 dB(A) |
Właściwy dobór kompresora śrubowego pod kątem wydajności, ciśnienia roboczego oraz poziomu hałasu ma kluczowe znaczenie dla efektywnej i bezpiecznej eksploatacji maszyn CNC.
wybór systemu chłodzenia CNC
Dokonując wyboru systemu chłodzenia do maszyny CNC, należy wziąć pod uwagę szereg istotnych czynników. Kluczowe jest, aby dobrać rozwiązanie, które optymalnie dopasuje się do Twoich potrzeb, zapewniając efektywne chłodzenie i długotrwałą, bezawaryjną pracę urządzenia.
Jednym z kluczowych zagadnień jest wydajność systemu chłodzenia. Musi on być w stanie skutecznie odprowadzać ciepło generowane podczas intensywnej obróbki CNC, utrzymując stabilną temperaturę w maszynie. Ważne są również takie parametry, jak kompatybilność z konkretnym modelem urządzenia czy koszty eksploatacji.
- Destylowana woda wymieniana raz na 2-3 tygodnie.
- Płyn chłodniczy wymieniany np. raz na 2 miesiące.
- Maksymalna temperatura cieczy chłodzącej wynosi 25-27 °C dla efektywnej pracy plotera laserowego CO2.
- Zwykła pompka wody wymaga częstej kontroli temperatury.
- Chillery CW3000 nadają się do ploterów o mocy do 60W.
- Chillery CW5200 i CW6200 nadają się do ploterów o mocy powyżej 150W.
- Chillery posiadające panel LCD umożliwiają ustawienie konkretnej temperatury cieczy chłodzącej.
- Pompka wody wystarczająca dla małych ploterów używanych sporadycznie.
- Chillery CW5200 i CW6200 zalecane dla intensywnej pracy plotera przez wiele godzin dziennie.
- Stabilna temperatura zapewnia powtarzalność lasera i sprawność tuby.
Dokonując wyboru systemu chłodzenia CNC, należy zatem starannie przeanalizować wszystkie istotne czynniki, aby dobrać rozwiązanie optymalnie dostosowane do specyfiki Twojego urządzenia i charakteru pracy. Tylko w ten sposób możesz zagwarantować efektywne chłodzenie, a co za tym idzie, niezawodne działanie maszyny CNC.
Wniosek
Właściwy wybór systemu chłodzenia jest kluczowy dla zapewnienia optymalnej wydajności maszyn CNC. Począwszy od prostych układów chłodzenia bezpośredniego, przez bardziej złożone rozwiązania chłodzenia pośredniego, aż po zaawansowane systemy chłodzenia oleju, istnieje wiele różnych opcji, które mogą być dostosowane do konkretnych potrzeb Twojego zakładu obróbki CNC.
Podczas dokonywania wyboru systemu chłodzenia warto skonsultować się z ekspertami, aby gruntownie przeanalizować wymagania Twojej firmy. Tylko wtedy będziesz w stanie podsumować wybór systemu chłodzenia CNC w sposób optymalny, zapewniając niezawodność, wydajność i długowieczność Twoich maszyn.
Niezależnie od wybranego rozwiązania, właściwe chłodzenie jest niezbędne do utrzymania optymalnej pracy Twoich maszyn CNC. Zainwestuj w system, który spełni Twoje oczekiwania i zapewni Ci długotrwałe korzyści dla Twojej działalności.
FAQ
Jakie są kluczowe czynniki przy wyborze systemu chłodzenia do maszyny CNC?
Kluczowymi czynnikami przy wyborze systemu chłodzenia do maszyny CNC są m.in. wymagana wydajność chłodzenia, kompatybilność z maszyną, a także koszty eksploatacji. Należy również wziąć pod uwagę takie aspekty jak rodzaj obrabianego materiału, czas pracy maszyny oraz parametry techniczne urządzenia.
Jakie są podstawowe rodzaje systemów chłodzenia maszyn CNC?
Podstawowe rodzaje systemów chłodzenia maszyn CNC to chłodzenie bezpośrednie (z wykorzystaniem powietrza) oraz chłodzenie pośrednie (z użyciem cieczy chłodzącej). Chłodzenie bezpośrednie opiera się na kształtowaniu żebrowania głowicy i cylindra, natomiast chłodzenie pośrednie wykorzystuje obieg cieczy chłodzącej przepływającej przez wymiennik ciepła.
Jakie są zalety chłodzenia pośredniego w maszynach CNC?
Chłodzenie pośrednie w maszynach CNC zapewnia bardziej stabilną temperaturę, co pozytywnie wpływa na żywotność maszyny i narzędzi. Głównymi elementami tego układu są: zbiornik na chłodziwo, pompa chłodziwa, przewody oraz dysze, które umożliwiają efektywne odprowadzanie ciepła.
Dlaczego chłodzenie oleju jest istotnym elementem dbałości o maszyny CNC?
Chłodzenie oleju pomaga utrzymać stałą temperaturę oleju, co zapewnia właściwe smarowanie i chłodzenie kluczowych komponentów maszyny CNC. Dzięki temu wydłuża się żywotność narzędzi i całej maszyny, a także zapobiega się jej przegrzewaniu. Systemy chłodzenia oleju działają na zasadzie przepływu oleju przez wymienniki ciepła, odprowadzając nadmiar ciepła na zewnątrz.
Jaką rolę odgrywają kompresory śrubowe przemysłowe we wspieraniu procesów obróbki CNC?
Kompresory śrubowe przemysłowe dostarczają niezawodne źródło sprężonego powietrza, które jest wykorzystywane do napędzania narzędzi pneumatycznych, systemów chłodzenia, usuwania wiórów i pyłu, a także do zaciskania i mocowania obrabianych przedmiotów. Odpowiedni dobór kompresora śrubowego ma kluczowe znaczenie dla wydajności i bezpieczeństwa maszyn CNC.